Sensors & Control Engineering
Control refers to the process of regulating or manipulating the behaviour of a system to achieve desired outcomes. In electro mechanisms, control plays a key role in managing and optimizing system performance. It aims at reducing the error of an actuator response compared to the input order.
At CTEC, the driver and the controller parts are always combined in the same single box or rack referred to as âThe controllerâ. The controller is based on microprocessor hardware with implemented digital control laws to allow fast, accurate and reliable computations.

Integrated in the control loop, the position sensor is a key element in a control loop to get a response from the mechanism output.
Sensors
As a standard practice at CTEC, we use strain gauges on our piezoelectric mechanisms. Directly bonded to the piezoelectric ceramic, the strain gauge allows for an indirect measurement of the mechanism’s movement through the deformation of the ceramic. These sensors offer the advantage of being compact and easily integrable. However, they have a limitation when the desired dynamic performance approaches the resonance frequency of the mechanism. The mechanical amplification of the resonance introduces an error between the expansion of the ceramics and the actual movement of the mechanism.
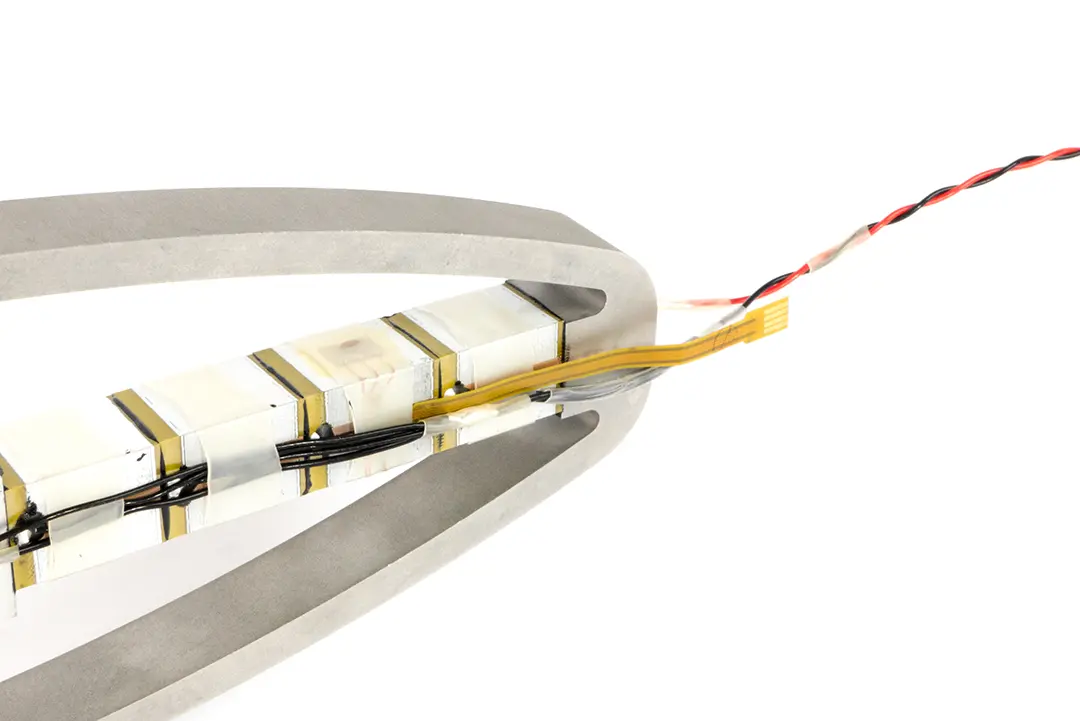
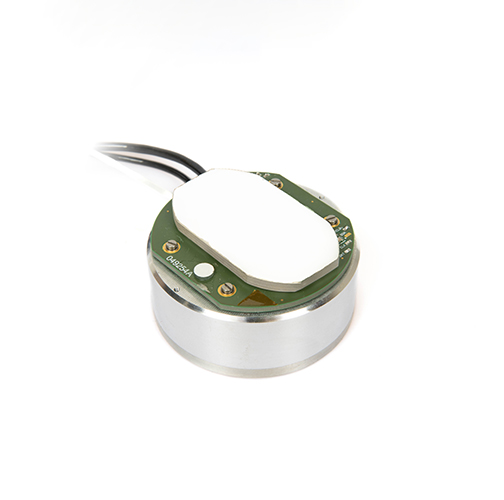
For demanding control requirements and magnetic mechanisms, CTEC utilizes Eddy Current Sensors (ECS sensors) to achieve a direct reading of the mechanism. This technology, combined with a more advanced control, allows us to precisely control our mechanisms even up to and beyond their resonance. However, this type of sensor requires more space and imposes additional integration constraints on the mechanism.
CTEC can customise its Eddy Current Sensor technology to suit your specific application: embedded linear or angular sensors, such as flat ECS on PCB placed below the mirror in FSM and DTT mechanisms  and micro switching sensing solutions for tangential and normal motion detection.
Control
Depending on the application and the aimed performances, control is customized for each specific development. The table below summarizes the error analysis needs for different applications:
Functions
Slow positioning
Fast positioning
Tracking
Rejection of vibration
Applications
Static
Dynamic
Dynamic
Dynamic
Analysed performances
Amplitude error
Combined error: Amplitude and phase error, jitter, settling time
Combined error: Amplitude and phase error, jitter, rising time
Jitter, rejection of disturbances
Examples
Slow payload motion or pointing, point ahead mechanism or positioner
Fast steering mirror, XY stage for micro-scanning, shutter
Fast steering mirror for line-of-sight stabilization or deblurring function
Fast steering mirror, proof mass damper
To reach the expected performances cited above, CTEC can design several types of control laws and implement them in its digital controllers. The fast mechanical response of CTEC mechanisms (thanks to their high mechanical resonant frequencies) requires very fast processing (few tens of kHz) which is the main difference with standard control of electric motor (few kHz).
Standard Control law based on PID & Notch filters cannot provide controller with the capability to react to external perturbations at resonance frequencies and above. An advanced control law based on full state feedback and model identification combined with correct sensors allows to damp these perturbation inputs at resonant frequencies of the system.
Preshaping could be associated with these feedback law to enhance overall performance.
Â
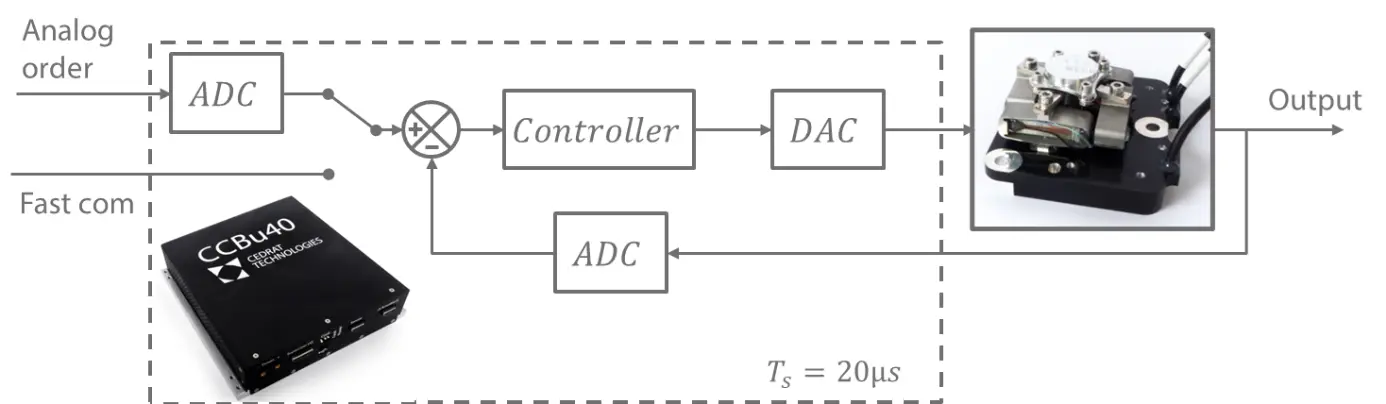
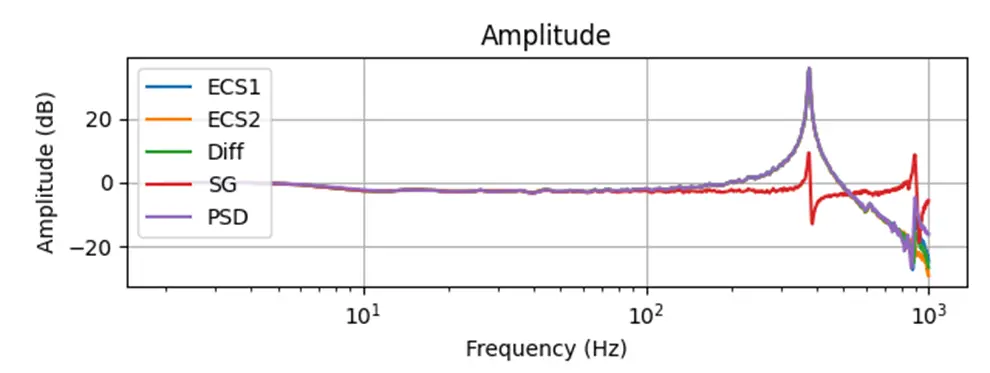
The dynamic of the system is directly improved: the cut off frequency is higher, and the system response time is shorter.
This figure shows the benefit of advanced control compared to standard PID.

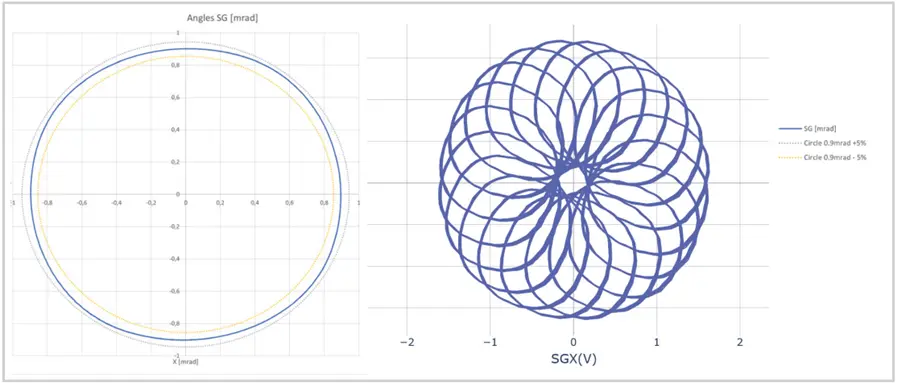
The dynamic response is highly improved resulting in more precise mechanism control, regardless of the signal shape.
Rapid prototyping could be used to demonstrate the performance of the control.
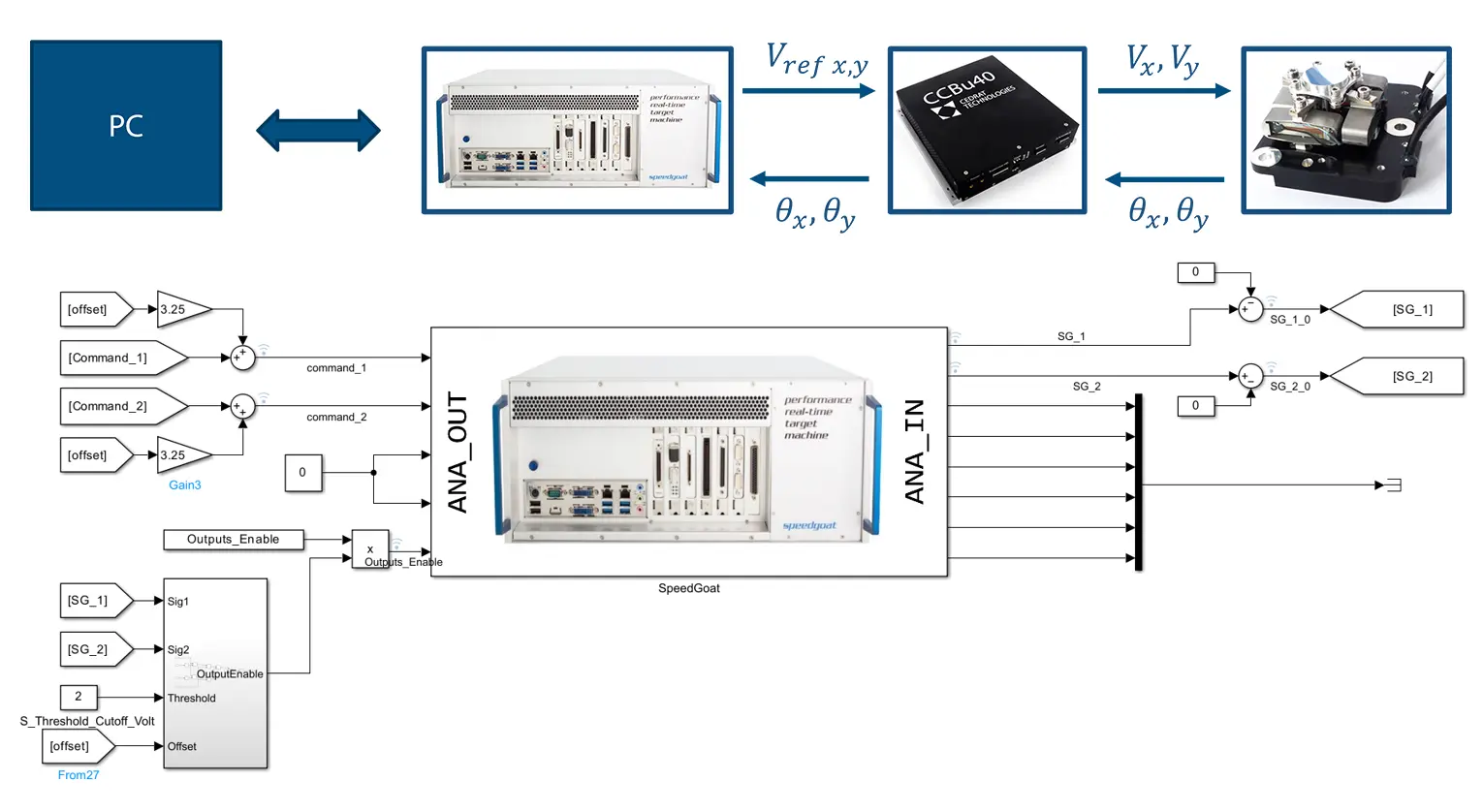
This type of advanced control can be implemented as part of a specific development process to achieve the highest performance. More information about our expertise in this area is available in our advanced control brochure.
The objective of the control team is to improve mechanisms speed and precision. When necessary, a focus could be made on developing new control laws to align with client performance needs. This involves identifying electromechanical models and implementing these control laws on digital platforms to ensure optimal performance and accuracy (using tools like Simulink, Mathlab, Speedgoat).
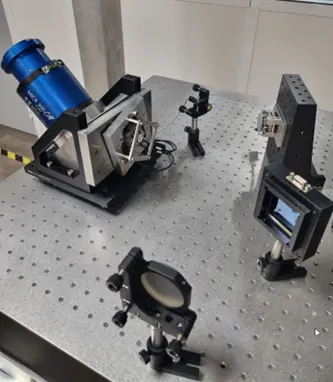