Publications
Categories
- (34)
- (9)
- (3)
- (144)
- (18)
- (7)
- (5)
- (8)
- (9)
- (17)
- (2)
- (104)
- (7)
- (15)
- (7)
- (2)
- (1)
- (6)
- (155)
- (20)
- (2)
- (5)
- (111)
- (35)
- (11)
- (4)
- (59)
- (18)
- (3)
- (7)
- (62)
- (18)
- (5)
- (24)
- (7)
- (12)
- (1)
- (2)
- (2)
- (1)
- (1)
- (14)
- (13)
- (4)
- (6)
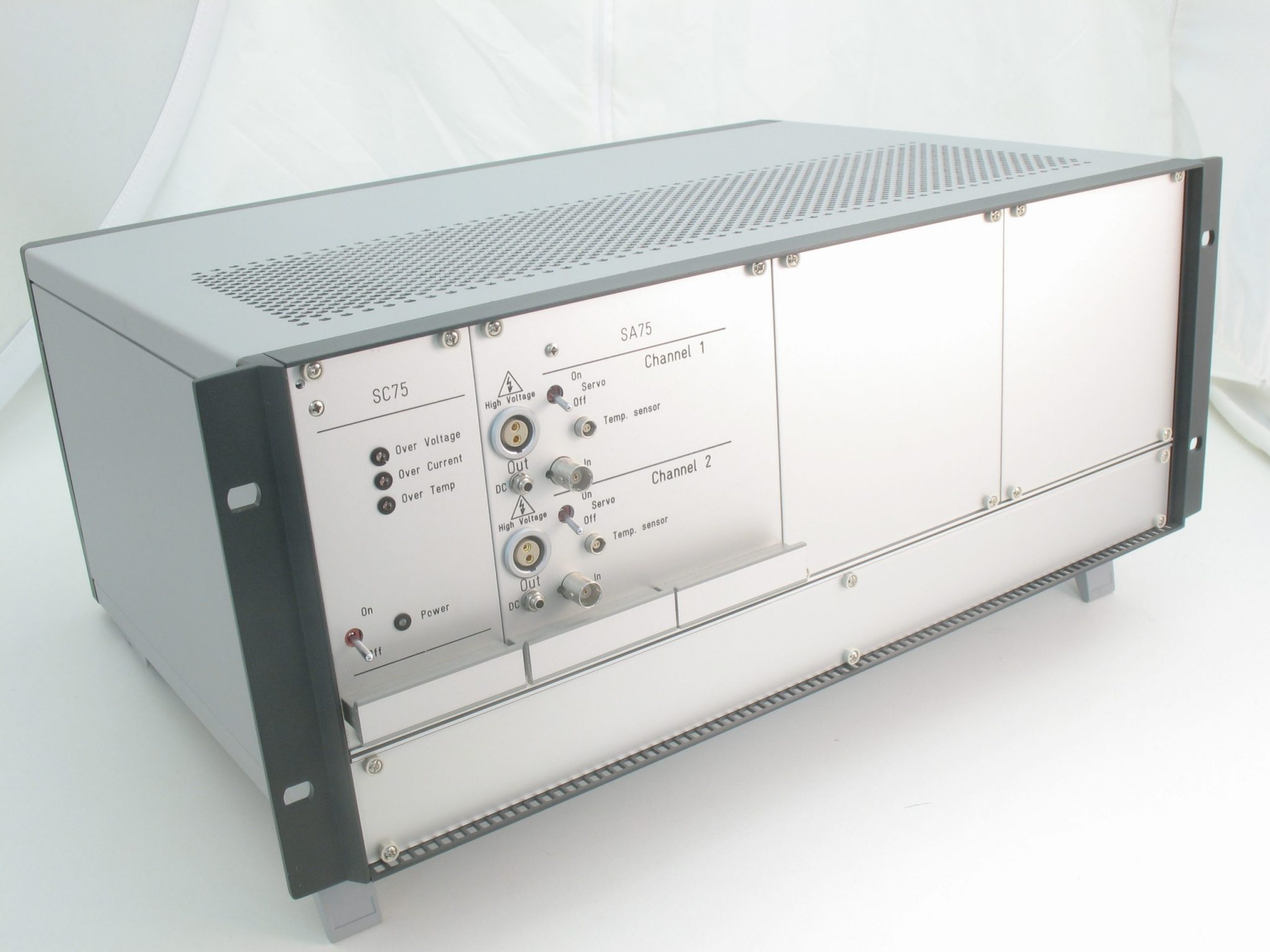
New Design of High Switching Power Amplifier for driving Piezoelectric Actuators in aeronautic applications
19 June 2023
Nowadays, piezoelectric actuators (PA) are used in fast power actuations and high power applications as requested in machine tools or helicopters flap applications. Regarding to the low power capability and high loss ratios of linear amplifiers, Switching Power Amplifiers (SA75X) is designed by Cedrat Technologies to drive piezoelectric actuators in such applications. The switching technique (up to 100 kHz) allows high current peaks required by impulse or by high frequency applications on large piezoelectric actuators (or actuators in parallel) and allows energy harvesting.
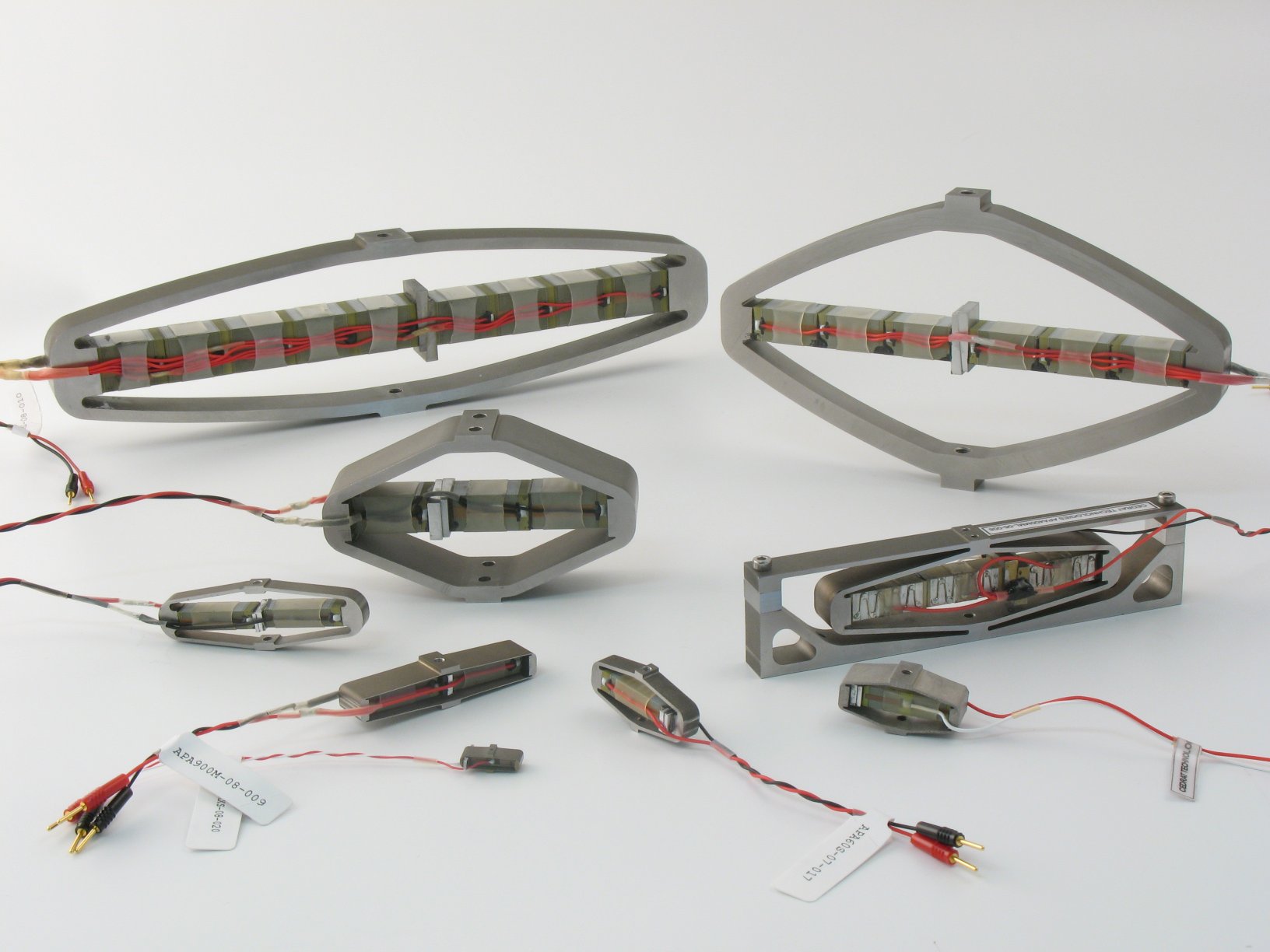
Amplified Piezoelectric Actuators:Static & Dynamic Applications
19 June 2023
Piezo actuators can be classified in three main categories: stack-type actuators, external/internal leveraged actuators and frequency-leveraged actuators (such as stepping motors and ultrasonic motors) [1]. Although Cedrat Technologies has developed several solutions using multilayered piezo ceramics and shell-based structures [2, 3], Amplified Piezo Actuators have today received the largest market interest.
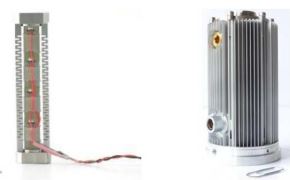
New developments in piezo actuators: Long stroke actuators and high power electronics
19 June 2023
In many cases piezoelectric actuators reach limitations in terms of maximum displacement and cycling frequency. Most amplified actuator technologies struggle to go over the millimeter of stroke. Furthermore certain closed-loop applications demand stroke measurement integrated into the actuator. While few amplifiers on the market can offer 20Amps current over a few 100ms, development of high power supply units runs parallel with actuator improvements. However with the introduction of high power supplies comes the problem of self-heating of the piezo ceramic. Finally extreme environmental conditions in terms of harsh conditions and high temperatures need to be addressed in order to open these markets for piezo actuators. Cedrat Technologies has been heavily investigating in solutions to overcome all of these drawbacks and these solutions are
presented here.
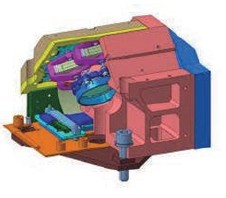
An improved accurate Beam Steering piezoelectric Mechanism for ATlid instrument
19 June 2023
A new tip tilt mechanism based on low voltage piezoelectric actuators has been designed by Cedrat Technologies to answer the high level of stability required for the Earthcare satellite. The Beam Steering Assembly aims to deviate a pulsed high energy UV laser beam to compensate for misalignment between the emission and reception paths of ATLID [1] with a very high stability and resolution. In this paper, the authors points out the BSM development with the main mechanism design issues including performances, mechanical and thermal stability; low power consumption; high integration level; high reliability and safety; cleanliness requirements and give the results of the qualification campaign done at Cedrat Technologiesâ to establish the final functional performances in preparation of the Flight Models deliveries for the BSM.
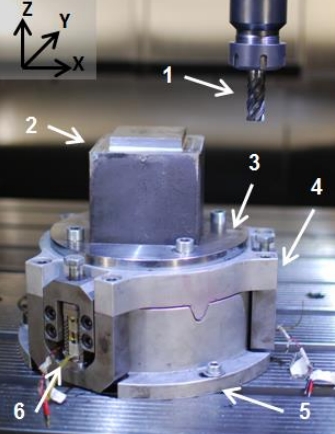
New Paradigm in control of machining system’s dynamics
19 June 2023
Complex mechanical components machined with zero defects are an essential condition in precision manufacturing and it becomes a new challenge for the next generation intelligent machining systems. Improved precision and accuracy of machines, processes and components offers substantial benefits to a wide range of applications from ultra-precision to mass customization with higher quality and better reliability. Within this context, this paper identifies critical problems that limit the performance of the machining system and address them by advancing novel solutions.
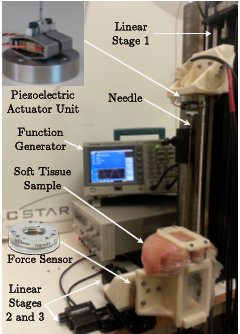
Analysis of NeedleâTissue Friction during Vibration-Assisted Needle Insertion
19 June 2023
In this paper, a vibration-assisted needle insertion technique has been proposed in order to reduce needleâtissue friction. The LuGre friction model was employed as a basis for the current study and the model was extended and analyzed to include the impact of high-frequency vibration on translational friction. Experiments were conducted to evaluate the role of insertion speed as well as vibration frequency on frictional effects. In the experiments conducted, an 18 GA brachytherapy needle was vibrated and inserted into an ex-vivo soft tissue sample using a pair of amplified piezoelectric actuators. Analysis demonstrates that the translational friction can be reduced by introducing a vibratory low-amplitude motion onto a regular insertion profile, which is usually performed at a constant rate.