Opto-mechanical Engineering
The integration of optical components into mechanisms has become essential in many sectors, particularly for scientific instrumentation, aerospace and defence: this is known as optronics. This need results from the demand for compact, precise and versatile optical systems. It is destined to address pointing and stabilisation functions. In order to meet new optical requirements while guaranteeing the system’s mechatronic performances, new constraints must be taken into account:
- The inertia generated by the size and mass of the mirror,
- The quality of the mirror surface,
- The self-heating of the mirror due to laser power.
CTEC has the capability, based on former space flight heritage methodology, at every stage of the project, to include the integration of optical elements:
Mirror Inertia
The inertia of the mirror has a direct impact on the rigidity, the stability of the mechanism it incorporates and its capacity to withstand vibrations and chocs. In general, optical quality has a negative impact on mirror inertia. It lowers the resonance frequency of the mechanism and thus reduces its dynamic and control performance. This trade-off is described in this brochure on our tip/tilt technologies. CTEC has the capability to include this problematic in your project through:
- FEM simulation to evaluate the loaded resonance frequency of the mechanism with the optical component and its resistance to your vibration’s environment. Our control team can also evaluate the expected performance and stability with the payload.
- Custom mirror design feasibility if needed in order to both answer your optical and control requirements (mirror shapes, ribs, material).
- Performances evaluation in laboratory through tests with dummy load or real mirror for control performances validation, vibrations and chocs qualification.
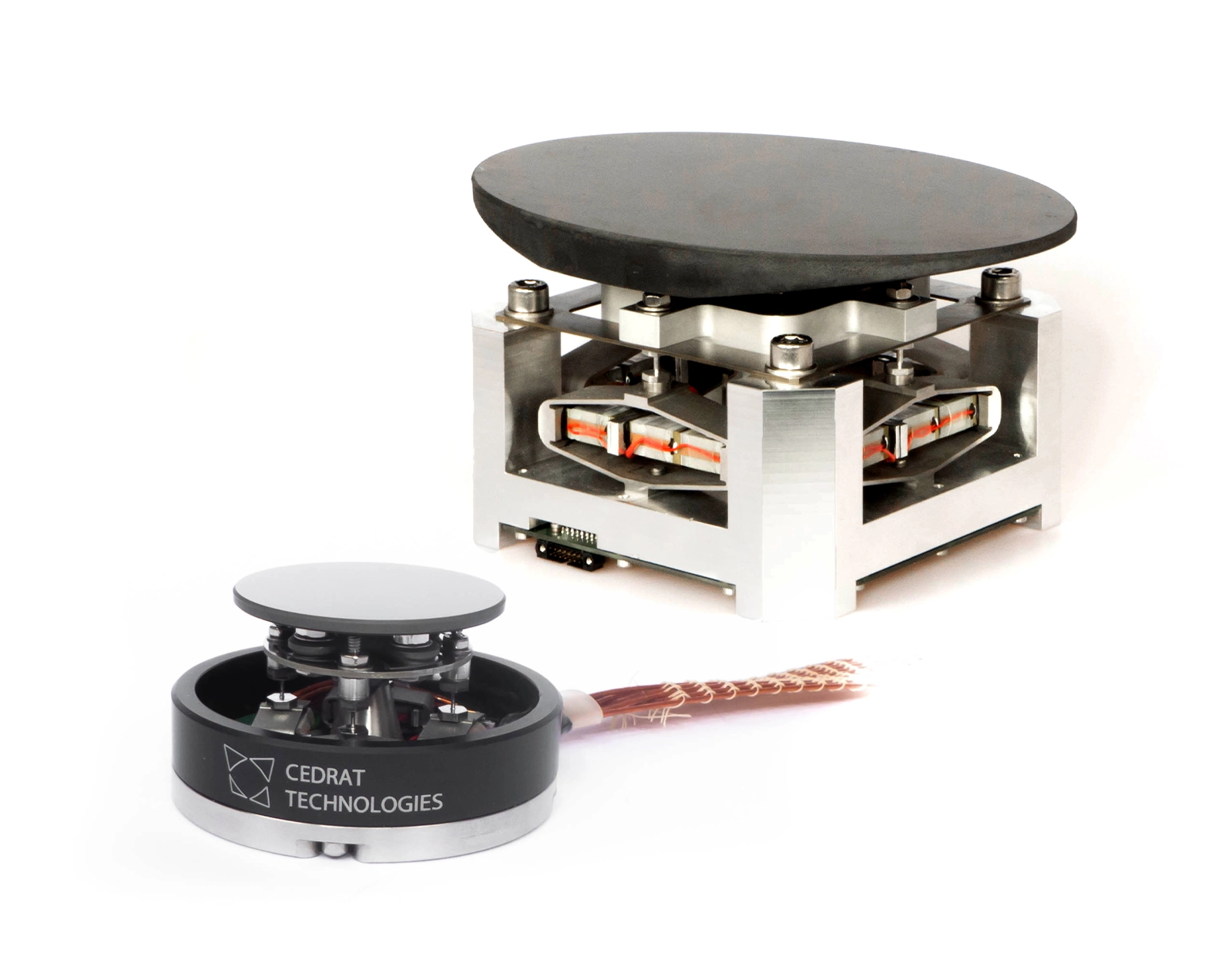
Mirror Quality
High-quality mirrors are required for precise laser and light handling, such as imaging instrumentations, optical communication and scientific instruments. Optical property such as mirror flatness can be significantly impacted during integration onto the mechanism. CTEC has the capability to include this problematic in your project through:
- FEM simulation to evaluate the effects of mechanical bias of integration and the effects of the actuators loads on the mirror flatness.
- Custom mirror and support design if needed to reduce the mirror deformation (flexible mirror support, integration techniques: screw, glue).
- Mirror wave front error evaluation at reception from the supplier and after integration to guarantee the optical properties (Zygo interferometer for Reflected Wave front Error RWE measurements).
Mirror Heating
Optronic applications require more and more laser power to improve their performances. It results in an increased need of high reflectivity coating and a self-heating evaluation to prevent components from overheating. CTEC has the capability to include this problematic in your project through:
- FEM simulation to evaluate the mirror self-heating due to the laser power absorption. Leading to temperature elevation and mirror deformation due to thermal expansion.
- Custom mirror and support design with adapted materials to reduce thermal expansion mismatch. Thermal drain technic can also be proposed for self-heating management.
- Thermal test with CTEC laboratory facilities and temperature monitoring to validate the design.
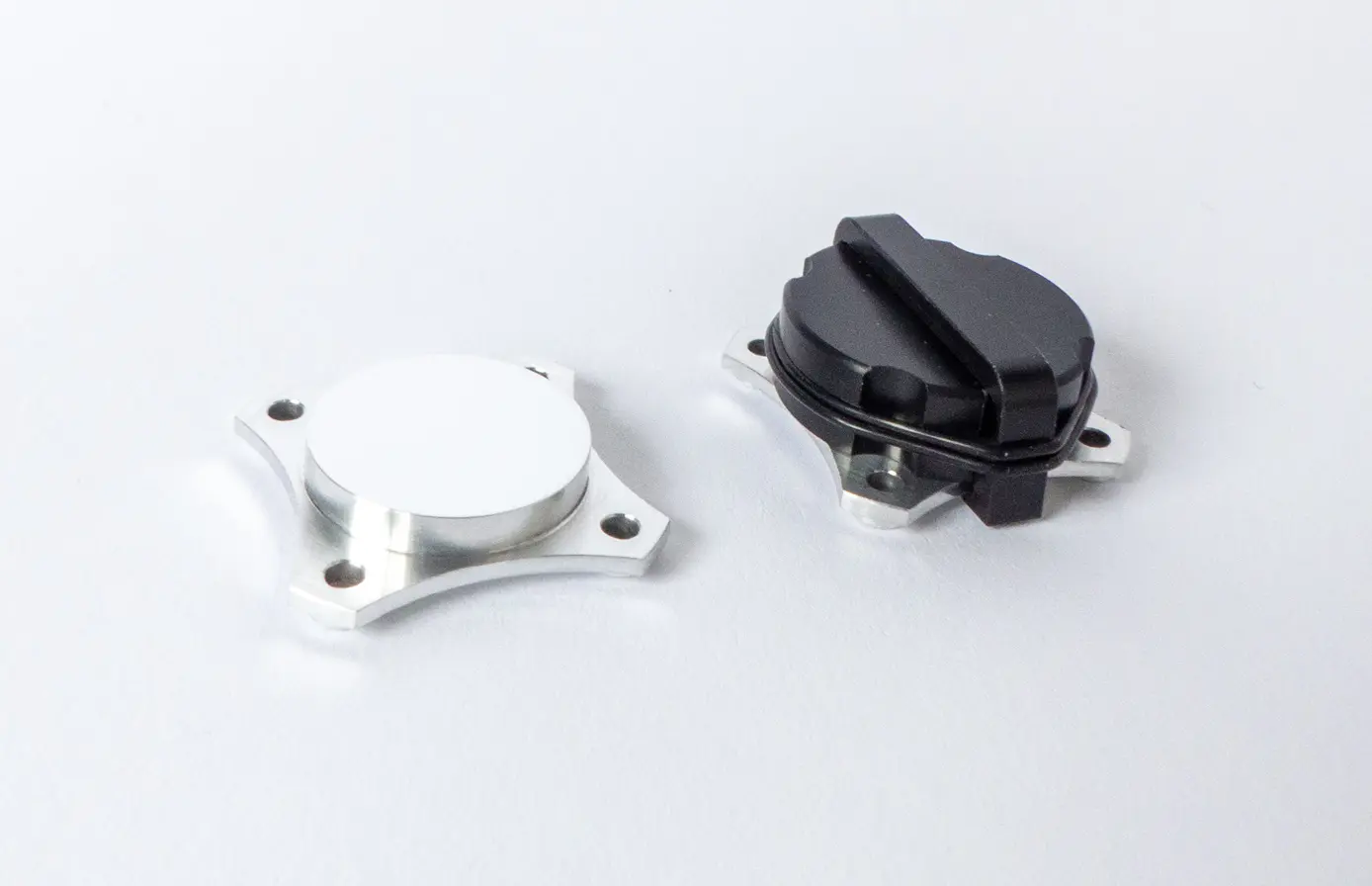
Substrate and coating
We have been working for a long time with our mirror suppliers and coating manufacturers, with whom we develop optical components in co-design to best meet the customer’s needs. We are used to work with substrates such as silicon carbide, fused silica, and other. Supply chains have been established with our suppliers. For challenging specifications on optical components, breadboard can be realized to measure and validate optical performances before committing with a qualified model.
CTEC has the capability to integrate your optical components while considering how the mechanism will impact the optical properties, through simulation in both electromechanical and thermal analysis. We work in close collaboration with our mirror partners in order to design the best opto-mechanical solutions.