Mechanism Engineering
CTEC develops and produces custom piezoelectric and magnetic mechanisms dedicated to its clients’ applications. With over 25 years of experience in the field, CTEC’s engineering teams are capable of meeting demanding and specific requirements in terms of advanced performances and severe environments. Below is presented typical roadmap steps for collaboration on industrial projects. The project flow and milestones can also be adapted to meet your specific needs. Project monitoring can range from simple studies to complex space projects.
Typical project roadmap
Feasibility and pre-design
To address needs not covered by COTS (Commercial Off-The-Shelf) products, CTEC initiates custom projects with a feasibility study. This study involves technology investigation, analytic modeling and evaluation of expected performances (e.g., stroke, bandwidth, power, …). This first design iteration guides specification definition, anticipates challenges, and includes a technological trade-off to prioritize specifications and explore concepts.
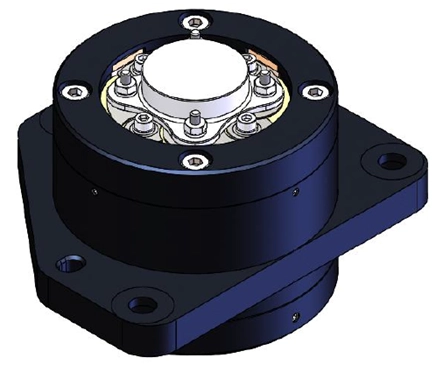
Piezoelectric and magnetic components are selected according to the application’s environment and the electric specifications. These technologies offer significant miniaturization capabilities, and the various sizes and power levels of available active materials, magnet or coil make it possible to address the same type of product with different scales and characteristics. Non-linear behavior and environment factors are also considered.
This process is conducted through technical meetings with the client, resulting in a compliance matrix, test plan, and risk assessment. A detailed proposal including a roadmap, work packages, planning, cost, and a preview of the final solution is then presented to the customer. This phase ensures a clear understanding of the customer’s needs, risk mitigation, and the proposal of viable engineering concepts aligned with specifications and market expectations.
Detailed design
Based on expertise in piezoelectric and magnetic engineering, CTEC offers advanced modeling and design services. Ranging from validating customer assumptions through single computations to conducting comprehensive optimization studies.
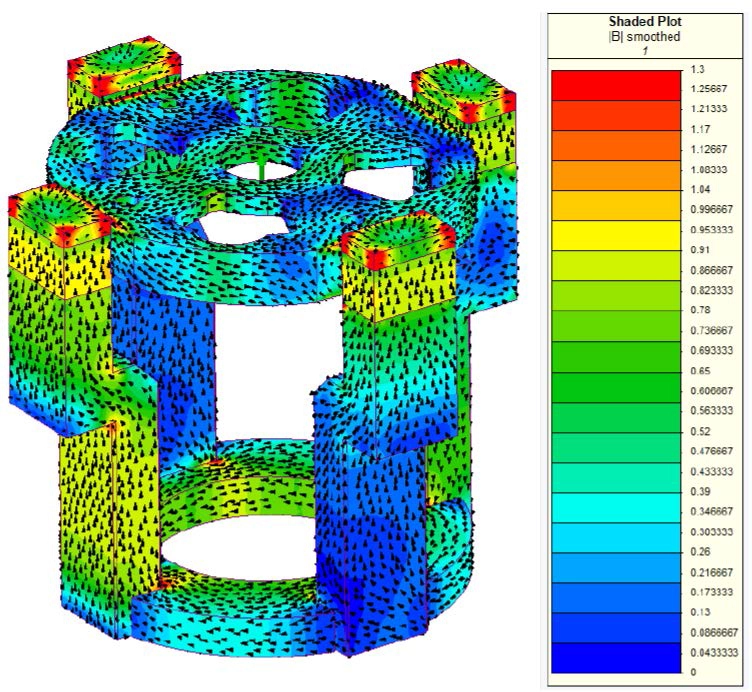
To develop new mechanisms our experts perform:
- Mechanical design with integrated CAD mechanisms and drawings on Solidworks (including actuators, sensors, PCBs and optical components),
- Multiphysics software for piezoelectric, magnetic and acoustic performances evaluation (NX Nastran, Flux, Magnet, ATILA),
- Mechanism performance evaluations to simulate control performances (for static, dynamic and ultrasonic application in opened and closed loops) using Solidworks, Simulink and Octave.
- Environmental performances for specific aerospace, defense and industrial applications (e.g., high temperatures, cryogenic conditions, vacuum, non-magnetic environment, vibrations, shocks, radiations) using Solidworks and NX Nastran.
Close collaboration is established between mechanical and electronic design during this phase. This includes task like integrating of nearby PCBs into the mechanical design and simulating control performances related to both the mechanism and electronics.
Manufacturing, Assembly, Integration, Testing (MAIT) & Qualification
CTEC makes use of breadboards and prototypes as rapid means to validate performances, remove technical risks of the project and ensure cost-effectiveness. Manufacturing of mechanical parts and active materials is subcontracted. Control upon reception and quality monitoring of our suppliers are realized. Then each component is assembled and tested in our electromechanical laboratory. For specific mechanisms such as FSM, challenging integrations can be performed (like mirror integration without deformation of the reflective surface).
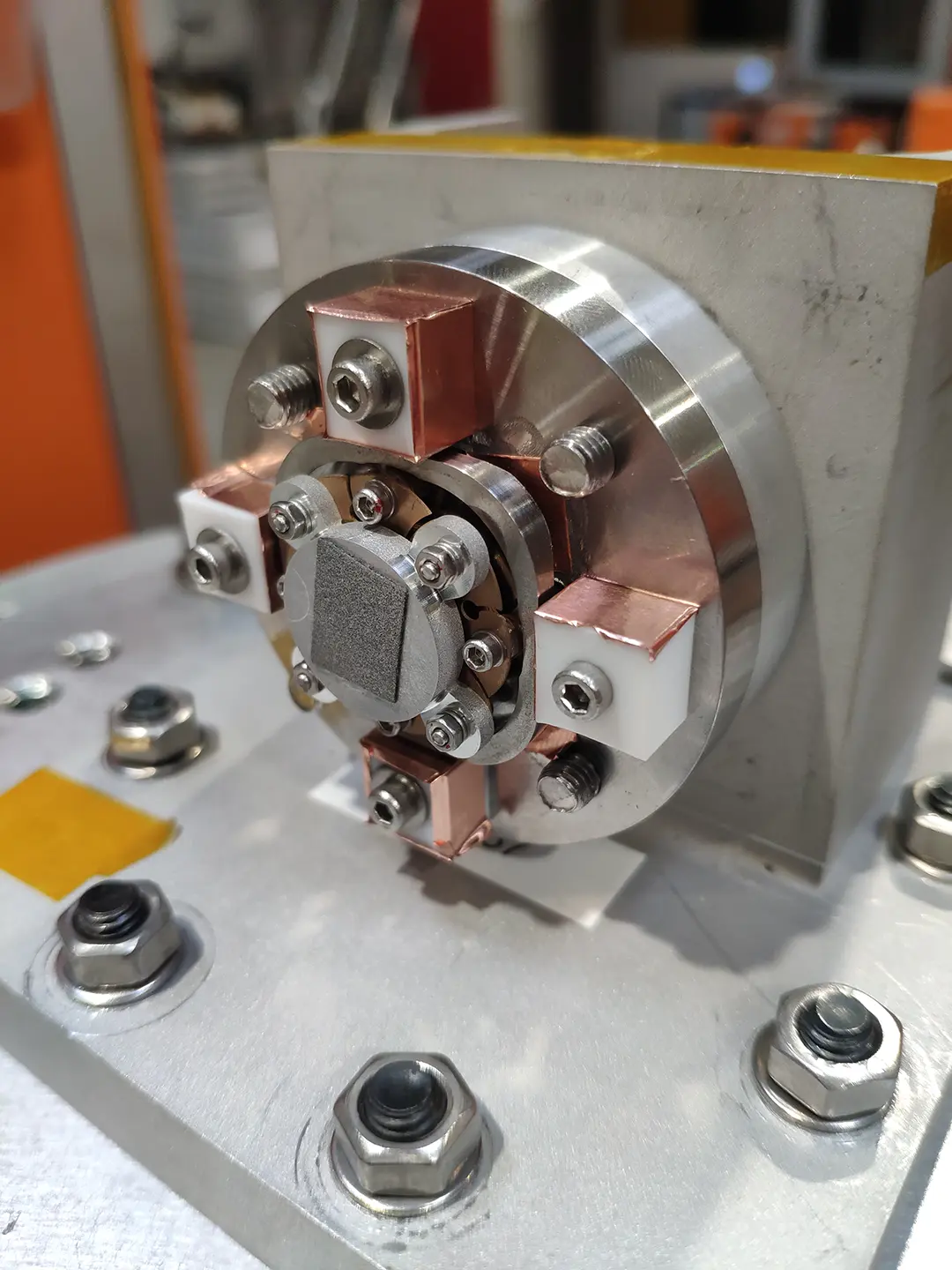
CTEC’s laboratory facilities include vacuum thermal chamber, shakers, interferometer, and various electronics, … to perform tests in order to validate the breadboard.
This 1st prototype is validated with a test report shared with the customer. It can lead to design optimization, the development of a qualification model for serial production.
Industrialization
CTEC is specialized in qualifying products for various markets and applications using its dedicated laboratory facilities for large-scale production. Our electromechanical design office provides internal support to the methods team for product industrialization. This includes assistance with defining assembly and transport tools, design to cost analysis and risk assessments.
More information about industrialization at CTEC is available on the industrialization webpage.
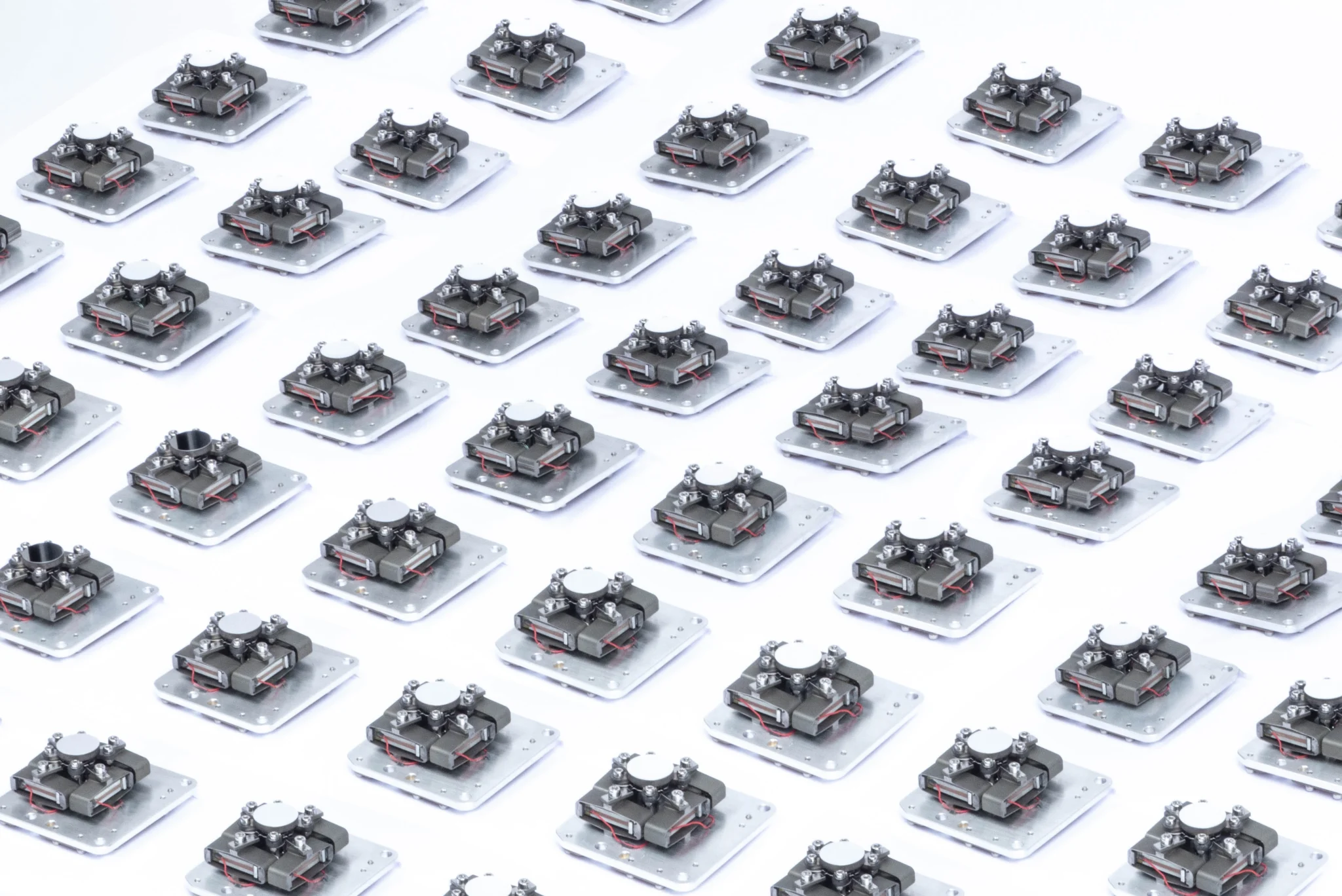
Aerospace and Newspace projects
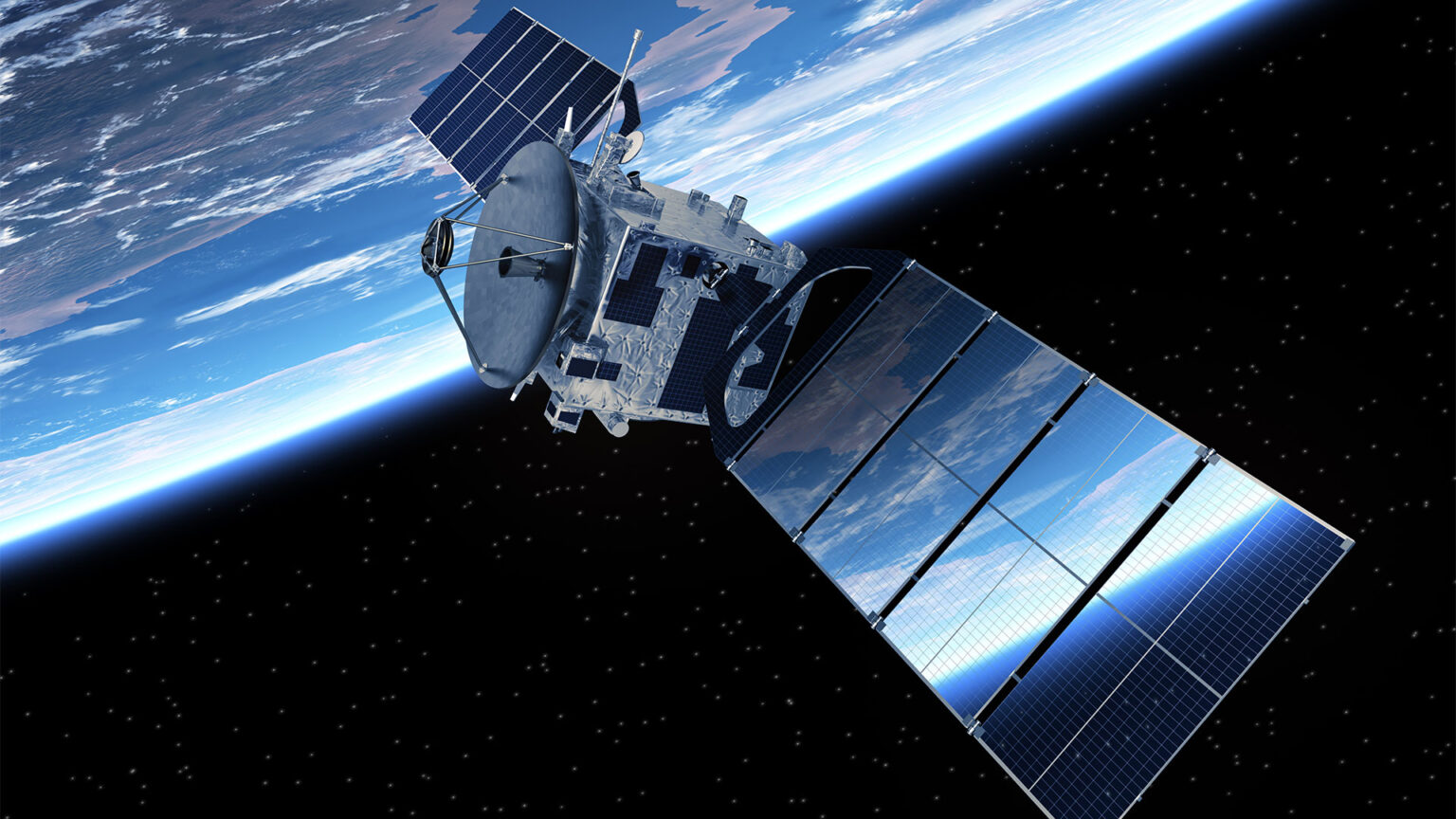
CTEC also has the capacity to address complex aerospace or low cost NewSpace projects. Based on years of experience in aerospace applications, CTEC’s designs comply with ECSS space standards and cleanliness specification. In addition, design justification reports and set up configurations can be provided.
CTEC complies with the usual qualification process of a space project:
- Engineering model fully tested with space-compatible materials.
- Qualification model, including vibrations, shocks, thermal vacuum, and lifetime tests.
- Flight model.
This process underscores CTEC’s commitment to delivering high-quality solutions. Significantly, CTEC has delivered several thousand of piezoelectric actuators as space flight/qualification models, and engineering models have been provided to esteemed clients.
Testing capacity
CTEC has the capability to develop our own specific test benches for your prototypes and products. These benches aim at meeting our clients’ performance and environmental qualification requirements. They combine several areas of expertise, such as:
- Mechanics for measuring force, torque, stroke and speed,
- Coding skills to develop automated test benches on Python,
- Opto-mechanics for detecting integration bias in our mechanisms,
- Thermodynamics to measure the heat generated and resistance of our products to high and cryogenic temperature,
- Electronics and control for tuning feedback loops and measuring errors,
- Fluid dynamics to test our valves under high pressure,
- Micro-vibrations for measuring the emissions of our mechanisms in their environment,
- Ultrasonics for measuring our transducer efficiency and the generated gains.
Active and smart materials
CTEC has capitalized on various brand of piezoelectric and magnetic materials.
CTEC uses low voltage multilayer ceramics (150V) in its standard products and for specific projects, very low voltage ceramic (60V or 75V) or very high voltage (1000V). With over 30 years of experience in multilayer ceramic characterization (available from Europe and Asia), CTEC has been involved in prestigious projects in aerospace and nuclear fusion industries. This extensive experience has provided CTEC with deep insight into ceramic behavior in diverse environments and applications. CTEC’s experts share this knowledge through piezo and magnetic training, helping clients to better understand and use these technologies.
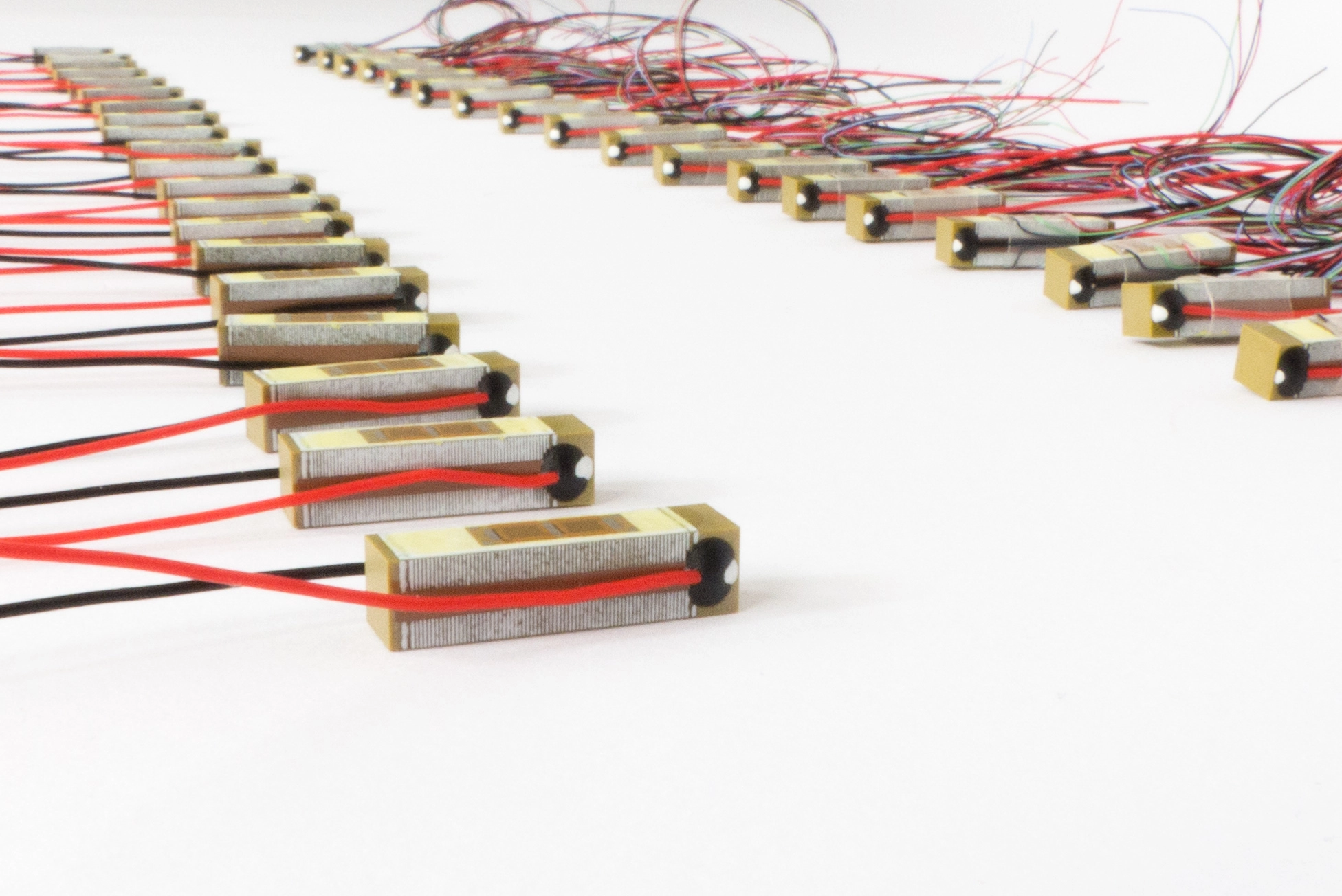
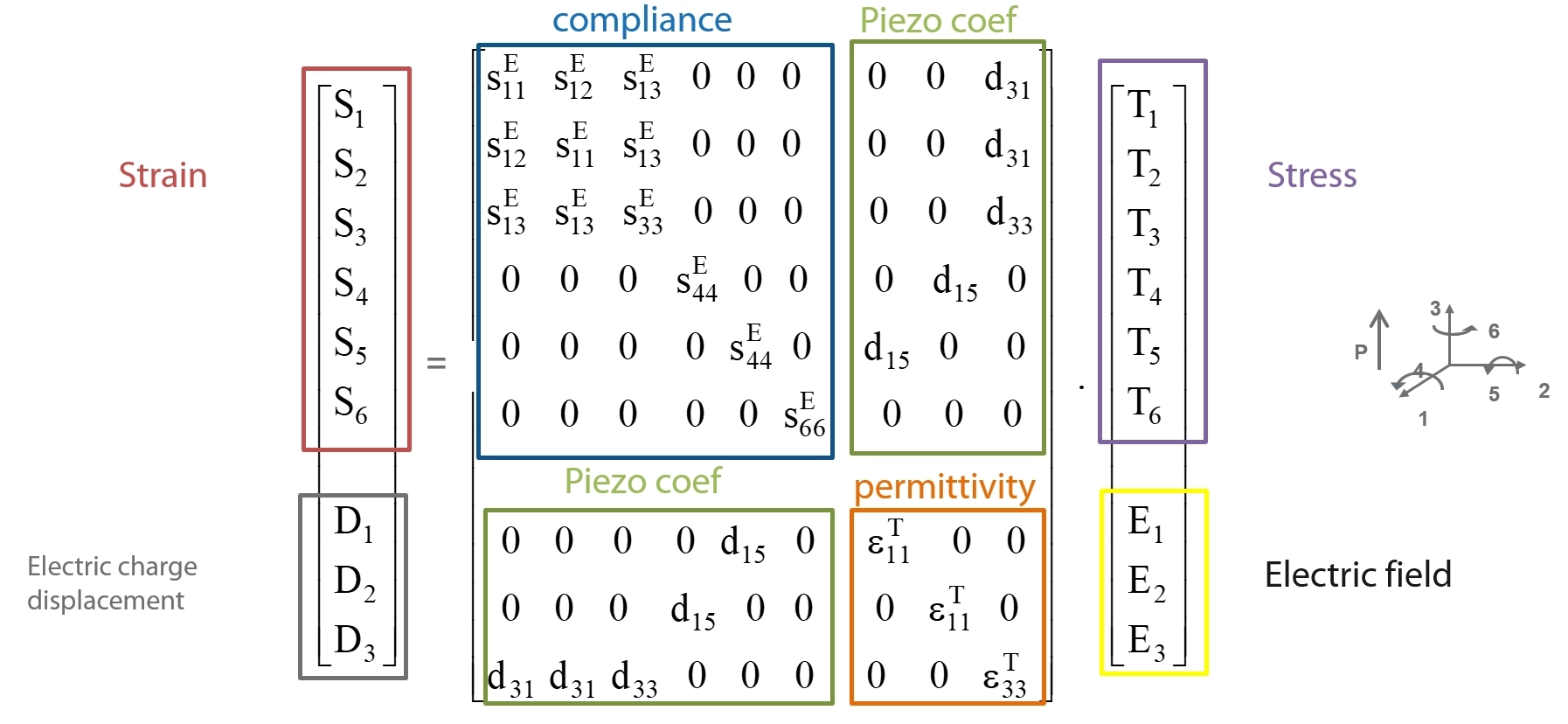
The following figures represent a cross-section of magnetic linear actuator with potted coils and piezo ceramic produced in collaboration with CNES. For more information on piezoelectric ceramic, please refer to chapter 2.1.2. of the catalogue. Destructive Physical Analysis (DPA) are performed on both piezoelectric and magnetic mechanisms to better understand their internal structure (that differs for piezo ceramic) and to validate our potting process for coil protection.
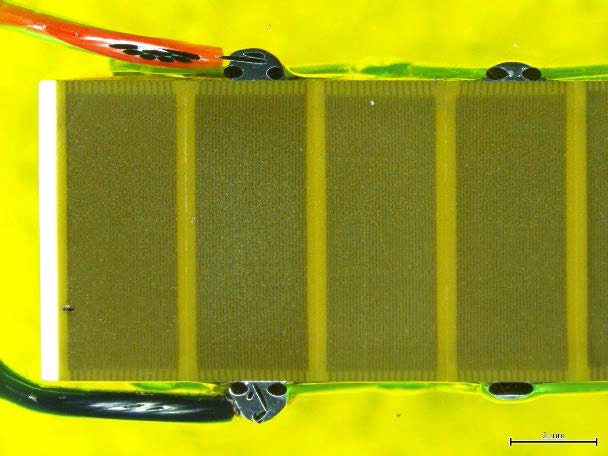
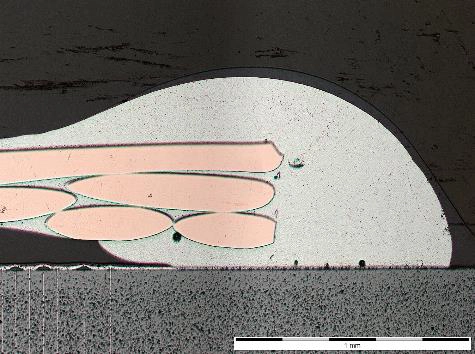
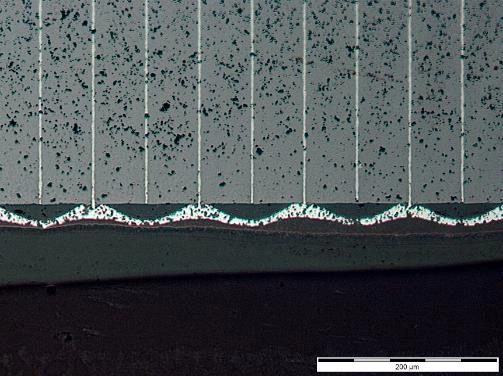
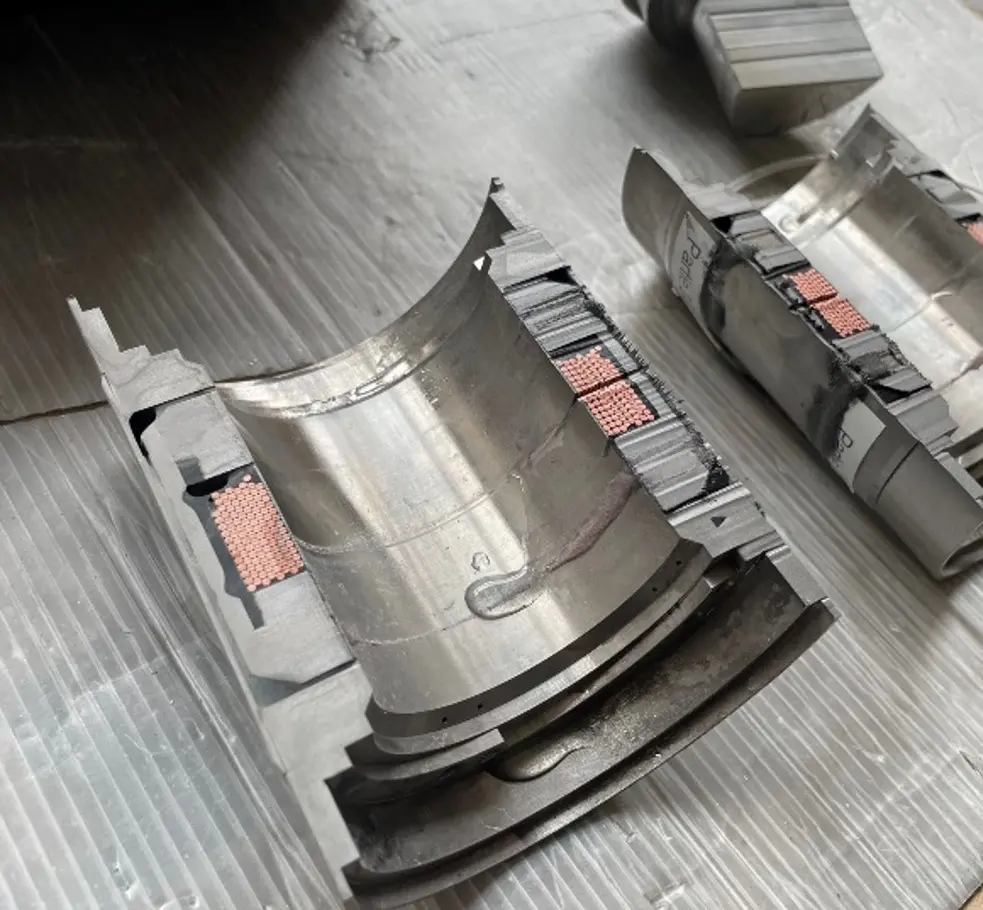
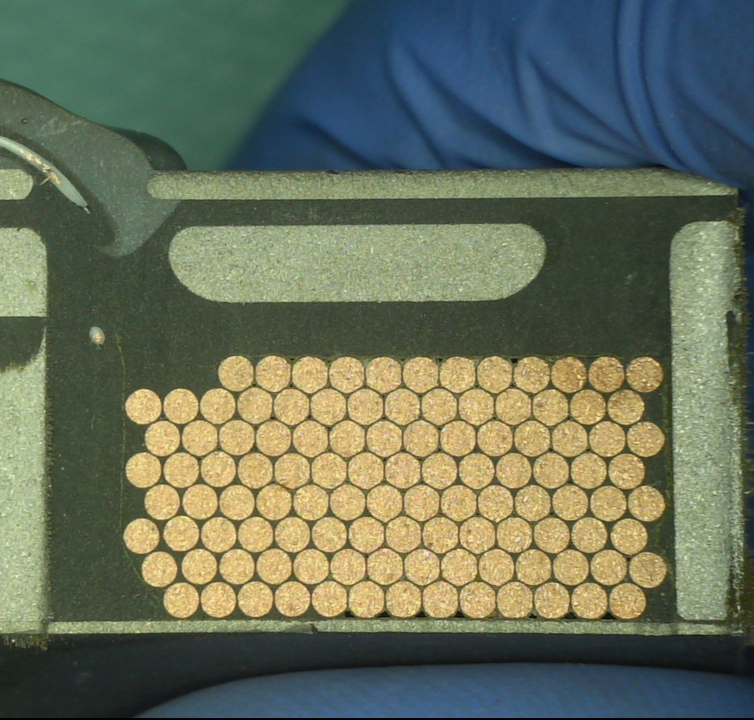