Industrialization
In addition to offering custom product development services, Cedrat Technologies specializes in small and medium-scale industrialization of its initial prototypes. We transform innovative concepts into industrialized products, with compact, integrated designs while ensuring quality and cost optimization.
How we achieve industrialization?
Industrialization is a collaborative and integrated process that begins as soon as a recurring production need is identified. Rather than focusing on individual components we adopt a global approach across the entire industrial flow. This enables us to streamline the production flow and avoid redundant or non-necessary steps. The process involves close collaboration between our design office and methods team. From the start they collaborate to refine processes (design for manufacturing), assemblies, tools, and ergonomic aspect). For instance, we create detailed work instructions outlining the manufacturing and assembly steps to ensure consistency and efficiency.
Our goal is to ensure:
- Traceability of every finished product with serial numbers (components, workforce, date, etc…).
- Cost efficiency production and cost-effective components.
- Volume production readiness by addressing critical challenges upfront, ensuring smooth production without later adjustments.
All the industrial work is adjusted accordingly to the production volume in order to optimise the project cost.
Extensive production facilities
Our industrialization relies on a large production and methods team equipped with all the necessary facilities to assemble and test our mechanism. It allows to optimise the production flows from cleanroom to the industrial environment. Significantly, CTEC has delivered several thousand of piezoelectric actuators as space flight/qualification models, and engineering models have been provided to esteemed clients.
In 2022, the company expanded its production facilities, featuring a certified ISO7 clean room of more than 100m² with an additional ISO5 cleanliness area spanning 10m². These facilities enable the realization of medium-sized recurrent series. In case of mass production need, please contact our sales engineers.
Our components require to master Electrostatic Discharge (EDS) issues through:
- ESD-safe workstation (grounded mats, wrist straps, …)
- ESD-safe floors (static-dissipative floors, operators equipped with ESD-safe footwear)
- ESD-safe packaging (anti-static packaging)
- Personnel training (proper handling techniques, regular audits)
- ESD tools and equipment controls
Expertise in manufacturing and testing
Our industrialization process is built on specialized know-how in:
- Development of our own process: we design our own processes and tools to assemble and test our products at an industrial pace uncompromising their technical imperatives.
- Advanced manufacturing techniques such as strain gauge bonding and mirror assembly, ensuring precision in every component.
- Complex assemblies: we handle complex mechanisms such as actuators, motors or fast steering mirrors while adhering to our assembly standards to ensure optimal product performance.
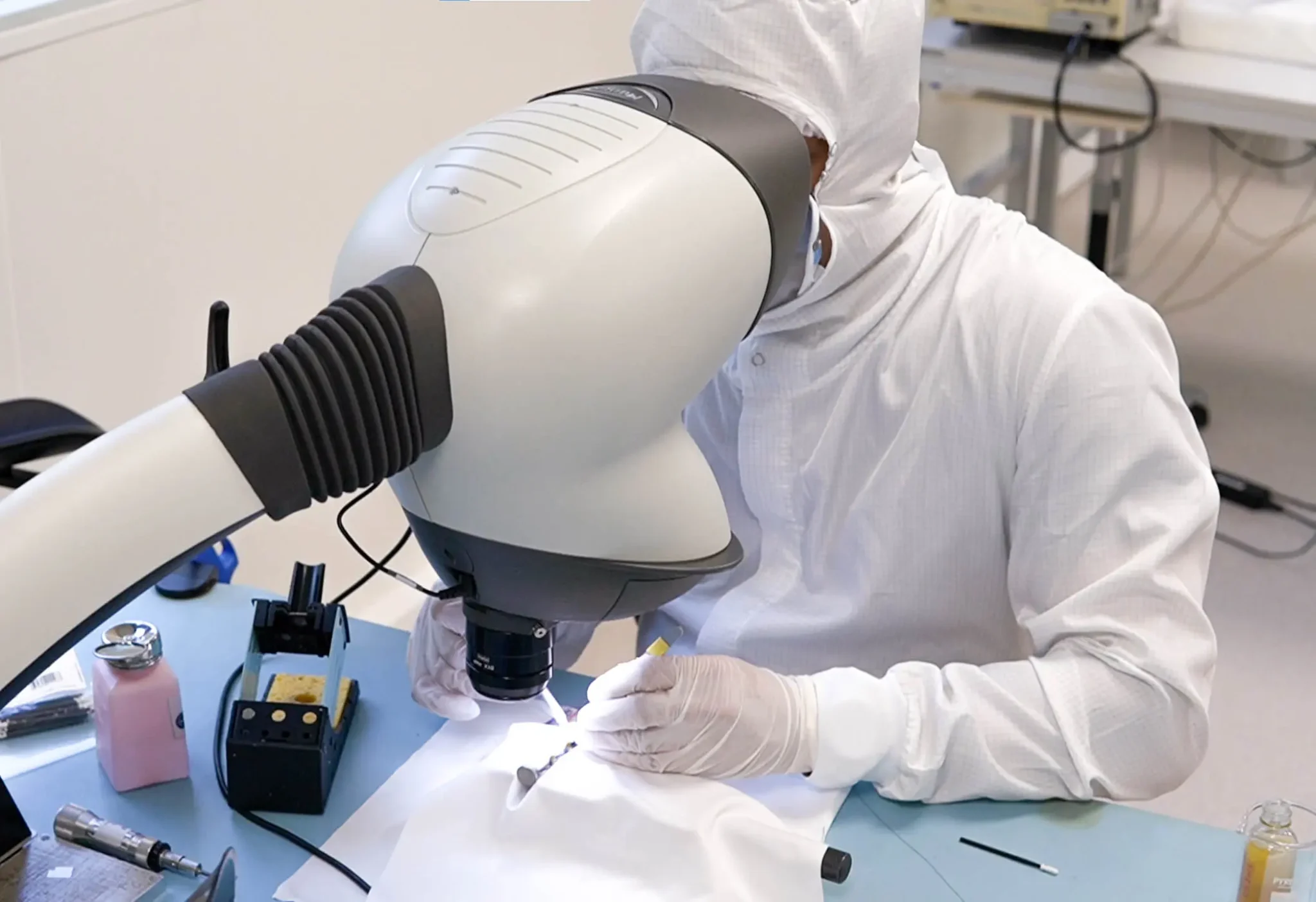
Industrial tool: ERP (Enterprise Resource Planning)
Thanks to our ERP we centralize all information from various services into a single platform. This allows an access to the same information in real-time for everyone. The ERP system includes all data necessary to purchase, produce and deliver our products, allowing us to manage quality, cost and timelines of our activities
Stock and supply chain management
We control the supply chain to prevent stock shortages and ensure that components are available when needed. This includes setting order thresholds, automating reorder suggestions, and managing supplier lead times.
By defining production schedules and cadences, such as batches of several dozens of units, we maintain a stable production rhythm. Retroactive planning helps us manage recurring orders to meet demand without overstocking.
After-sales service (SAV) management
Our Return Material Authorization (RMA) system ensures that recurring production issues are resolved efficiently. The Quality team is in charge of the RMA process, and depending on the issue, it can also involve either the production, the method or the design teams. Clients fill out a troubleshooting form that generates a production order for repair. After inspecting the product and identifying the issue, we validate our findings with the client and proceed with either warranty or non-warranty repair.
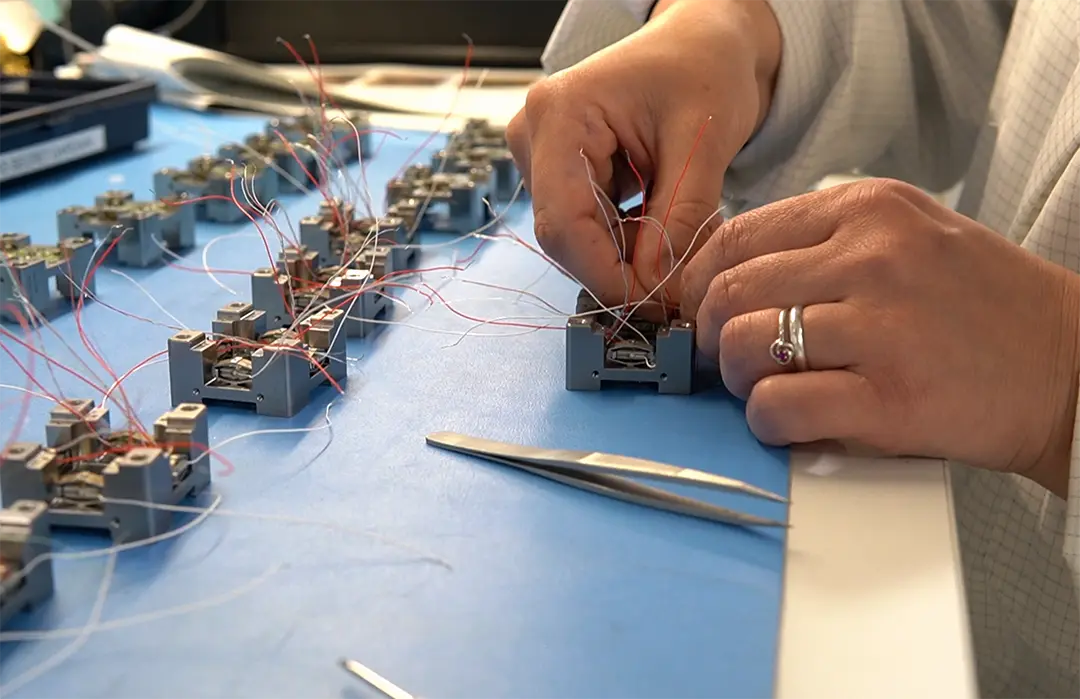
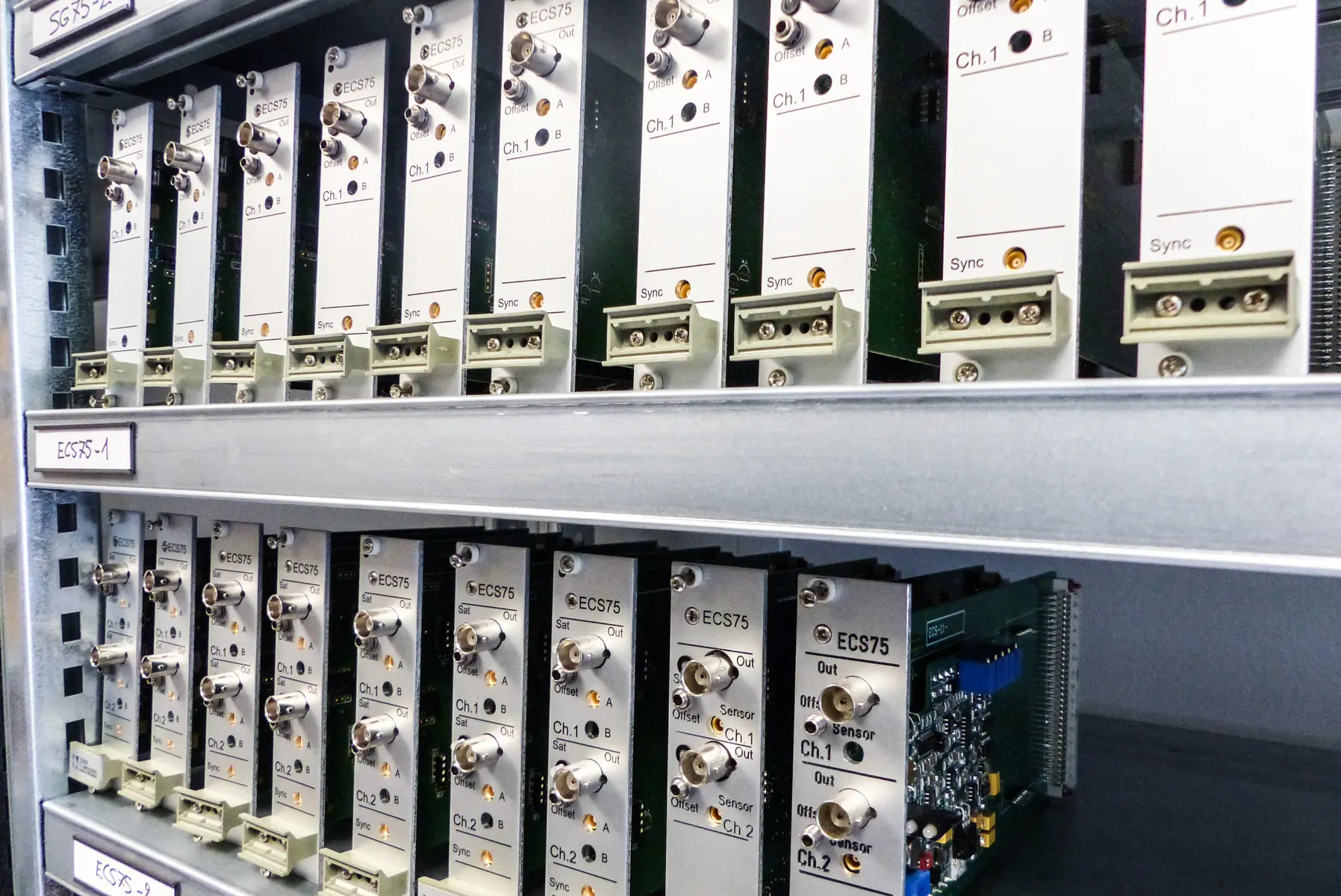