Driving Electronics Engineering
CTEC is specialized in the development of electronics for controlling mechanisms and conditioning sensors within complex digital architectures, including deterministic and fast communications. Our team of engineers has over 25 years of experience in designing electronic products across various disciplines.
Our development and design activities enable us to offer architectures incorporating high-efficiency power electronics, precise sensor low-noise conditioning, firmware around processors capable of supporting advanced control laws and performing complex calculations in the order of tens of microseconds. Our developments can be integrated at any stage of your project or lead to an industrialization phase.
Electronics modelling
The initial phase of designing specific driving electronics involves analyzing transient and time-domain electrical behaviors. This step lays the foundation for understanding how the electronics will perform in real situations. Operational thermal effects are included to guarantee the performances and reliability of the electronics under various types of use, specific application and mechanism. Depending on the environment, an evaluation of vibration effects and emitted electromagnetic fields may be conducted to ensure optimal performance and compliance with required standards.
In parallel, modelling the control behavior from basic control laws up to most recent robust controls is analyzed and errors in static or dynamic application are established.
Robust PID or specific model state controllers can be designed taken into account the application: static application, dynamic responses, tracking, rejection of vibration. Find more information on the control engineering dedicated webpage.
The strong interaction with mechanical engineers is involved to identify electromechanical parameters and establish the best solution to answer the client need. Fast prototyping with existing product can be implemented to established identification and performances in real time.
TOOLS: LTSPICE®, MATLAB®, SIMULINK®, SPEEDGOAT, SOLIDWORKS
SKILLS: Electronics modelling, robust control modelling, electromechanical identification
Electronic hardware design
CTEC defines in accordance with the client’s specification the architecture of complex electronics including drivers, sensors, microcontroller and communications.
Specific system architectures are developed including electronics in mechanisms and remote electronics to drive and control the system. Global error budgets are established to answer the requirements.
AC-DC converters using linear or switching technologies depending on the applications can be designed in regards of the required power and other factors such as efficiency, size constraints, and cost considerations.
Specific drivers are also designed in regards of the accuracy and signal integrity performance while respecting very compact mechanical dimensions.
Our design also takes into account different topologies of sensing solutions – Strain Gauges or contactless solution: low noise and accurate solutions can be developed taken into account the modelling phase results (observability concept – adapted solution like strain gauge integrated on the ceramic or proprietary Eddy current sensors). Grounding techniques, shielding, and filtering to minimize interference are adapted to reach the system performances.
For digital electronic design, CTEC selects their appropriate microcontrollers or microprocessor based on the sampling rate for processing, memory capacity, I/O capabilities. High sampling rate are involved up to few 10ks/s to implement dynamic control for large bandwidth while keeping stable and robust behaviors. Fast conversion and precise analog to digital and digital to analog converters can be implemented
Our electronics are opened to your host for rapid communication with digital bus.
TOOLS: ALTIUM365®, SOLIDWORKS,
SKILLS: System architecture, Power electronics, low noise electronics, DSP micro-controller, instrumentation, digital communication, electronic-mechanic Co design
Software – firmware development
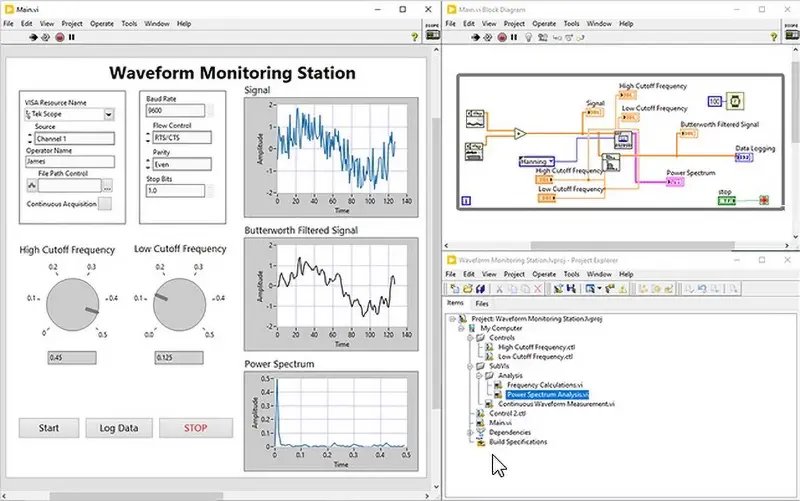
CTEC develops embedded software with ergonomic human-machine interface (HMI) in order to achieve robust control. The embedded code is done onto DSP platform which are able to support fast closed loop control.
Coding onto these platforms also take into account the global architecture and more precisely the control loops functions, the communications and the global functionalities as built in test, global monitoring.
In parallel, Human Machine Interface can be developed to communicate with the determinist embedded firmware. This HMI allows to operate with the system to change parameters and monitor the general behavior.
TOOLS: Specific development c platform
SKILLS: C, LABVIEW™, PYTHON™
Mechanical co-design for high integration
CTEC set up a collaborative co-design between electronic and mechanical engineering for developing a robust housing with specific packaging requirements adapted for severe environments such as MIL (Military) or space-grade applications.
CTEC can use flex, rigid, or multilayer printed circuit boards (PCBs).
Engineers from both domains work together to ensure that electronic components are integrated into mechanical structures while considering factors such as thermal management, shock and vibration resistance, and electromagnetic compatibility (EMC). This involves using reinforced casings, specific coatings, hermetic sealing, and advanced components resistant to large temperature variations, radiation, and vacuum.
TOOLS: MCAD Codesigner SOLIDWORKS, ALTIUM365®
SKILLS: Vibration, EMC, Thermal designs
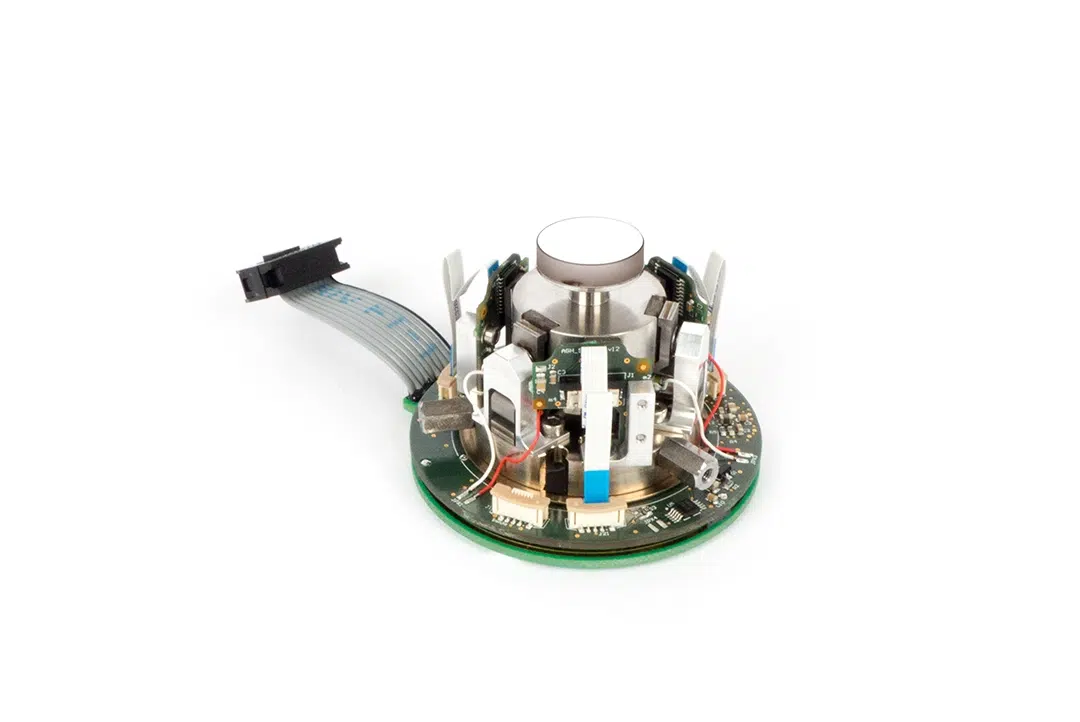
Assembly, Qualification & Acceptance testing
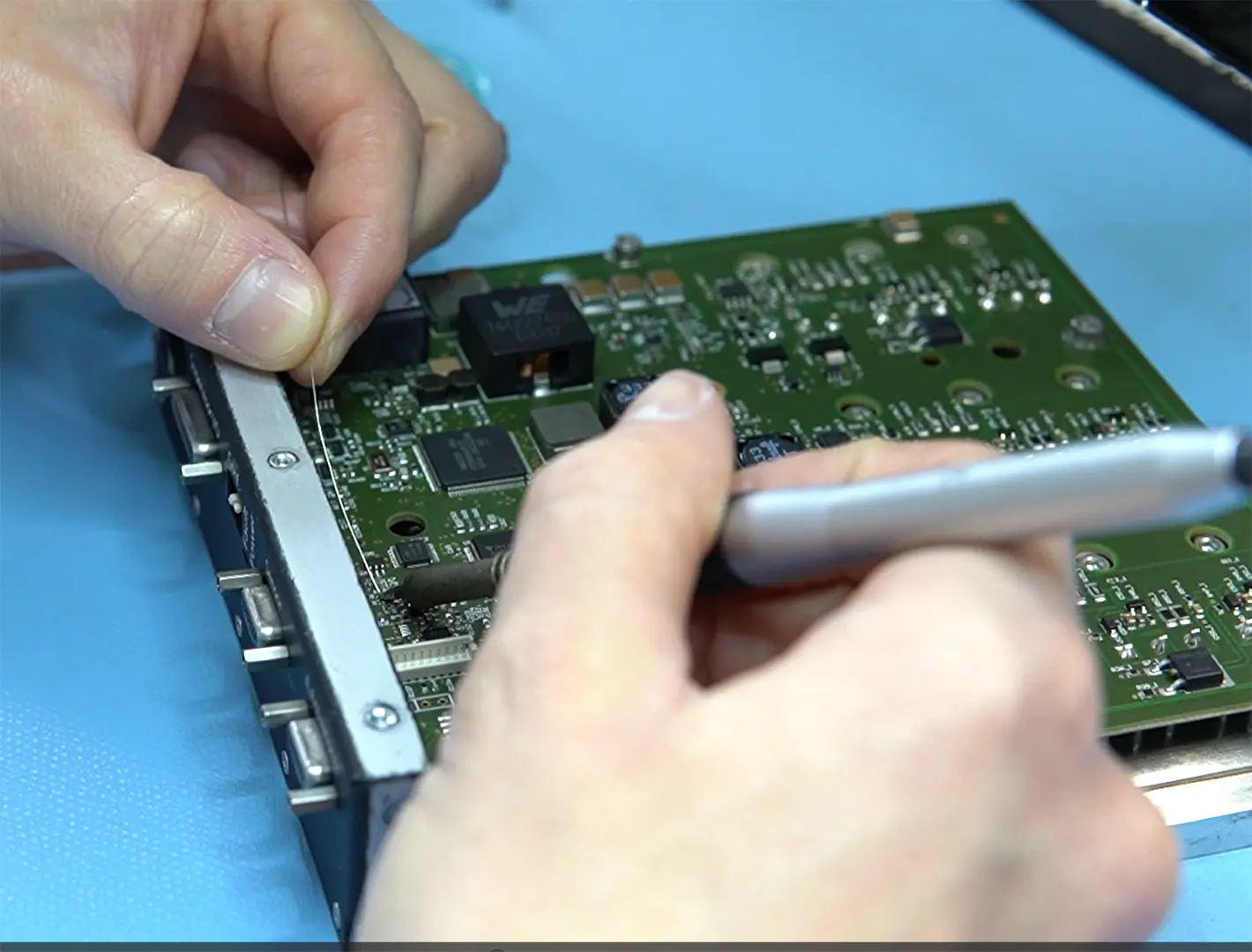
CTEC manufactures its product in accordance with IPC610 Class 2,3 and IPC620 Class 2,3 standards. Class 2 and Class 3 refer to different levels of acceptance criteria and workmanship standards, with Class 3 being the highest level of quality and reliability.
CTEC has received the ESA space soldering certification. Some operators have obtained this qualification and carry out the necessary trainings to maintain it.
For challenging requirements, our products go through a qualification tests plan to ensure reliability. These tests typically include thermal, shock & vibration, and electromagnetic compatibility (EMC) testing.
Acceptance testing involves verifying that manufactured electronic systems meet all specified requirements and standards before they are released for use or deployment.
TOOLS: Thermal chamber, vibration bench, Iso 5 area, electronics equipment,
SKILLS: instrumentation
Industrialization
At CTEC, industrialization for series production involves several key steps:
- Acceptance test benches to verify that manufactured electronic systems meet all specified requirements and standards.
- First Article Inspection (FAI) is a critical quality assurance process that involves inspecting the first manufactured unit.
- A Certificate of Conformity is then issued to certify that the product is conform.
In addition, obtaining CE, FCC certifications through the CB scheme is preferred for electronic products intended for sale in the world.
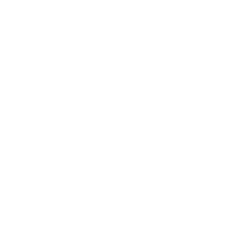
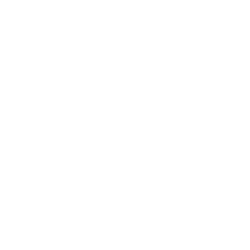
