Publications
Categories
- (34)
- (9)
- (3)
- (144)
- (18)
- (7)
- (5)
- (8)
- (9)
- (17)
- (2)
- (104)
- (7)
- (15)
- (7)
- (2)
- (1)
- (6)
- (155)
- (20)
- (2)
- (5)
- (111)
- (35)
- (11)
- (4)
- (59)
- (18)
- (3)
- (7)
- (62)
- (18)
- (5)
- (24)
- (7)
- (12)
- (1)
- (2)
- (2)
- (1)
- (1)
- (14)
- (13)
- (4)
- (6)
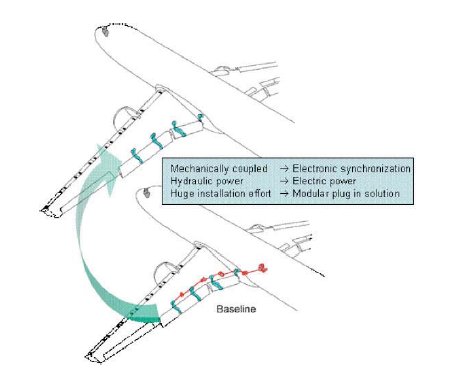
New actuators for aircraft and space applications
7 January 2008
Actuators are key elements of air- and spacecrafts. In the recent years the concept of the more-electric aircraft pushed the development of electrical actuation systems to substitute hitherto used hydraulic actuators in a broad range of applications such as flight control, landing gear and brake actuation.
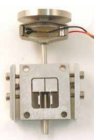
New actuators for aircraft, space and military applications
19 June 2023
Actuation is used in all vehicles (aircraft, spacecraft, ground vehicles, etc) to control the position and/or attitude of the vehicle, and also to deploy or retract equipment, particularly for embedded optic instruments (cameras, telescopes). As such, the actuation is a safety critical system, particularly when humans could be catastrophically affected by failures within the system. Applications for actuation are flight controls, landing gear, rotors, suspension, antennae steering, valves, scanning, positioning using hydraulic, electromechanical, magnetic and piezo actuators. In aircraft there is a common goal to reduce the number of hydraulic actuators in vehicles and eventually to replace them completely by electric actuators.
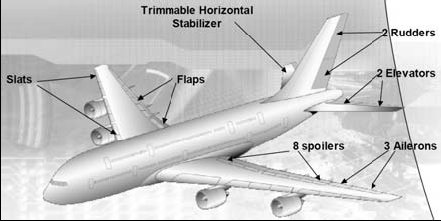
New actuators for space and aircraft applications
19 June 2023
Novel actuation systems are driver of product innovation in aerospace industry. In aircraft industry EHA technology has been recently introduced illustrating the stream of innovation directed on improving performance, reliability as well as economy. On the far side there is the radical concept of a morphing wing which offers optimizing the aerodynamics of an aircraft considerably by shape control. Rotor Active Control utilizing piezo actuation has been proofed to be very successful for vibration and noise reduction in helicopter flight test inspiring confidence in smart structure technology.
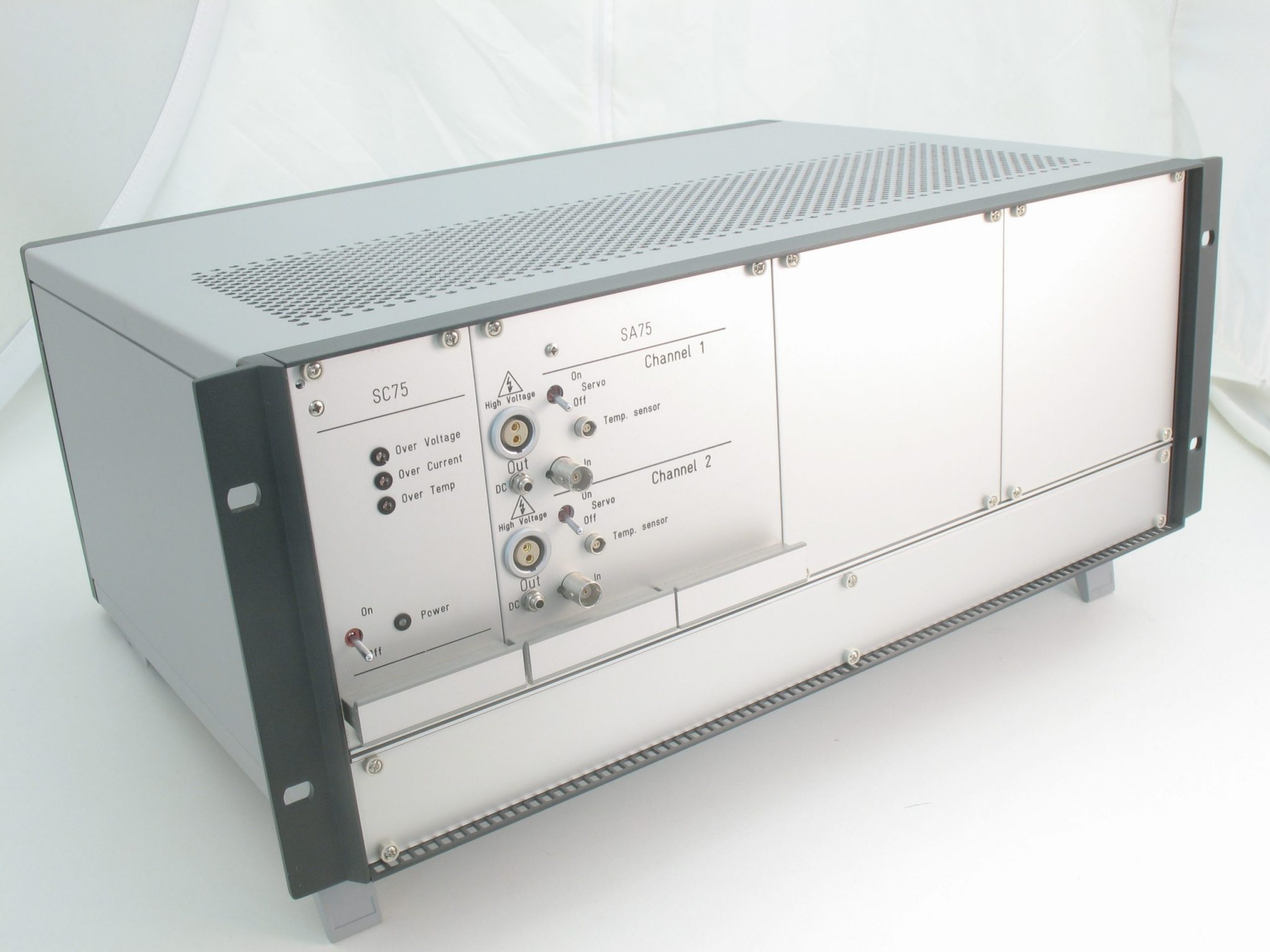
New Design of High Switching Power Amplifier for driving Piezoelectric Actuators in aeronautic applications
19 June 2023
Nowadays, piezoelectric actuators (PA) are used in fast power actuations and high power applications as requested in machine tools or helicopters flap applications. Regarding to the low power capability and high loss ratios of linear amplifiers, Switching Power Amplifiers (SA75X) is designed by Cedrat Technologies to drive piezoelectric actuators in such applications. The switching technique (up to 100 kHz) allows high current peaks required by impulse or by high frequency applications on large piezoelectric actuators (or actuators in parallel) and allows energy harvesting.
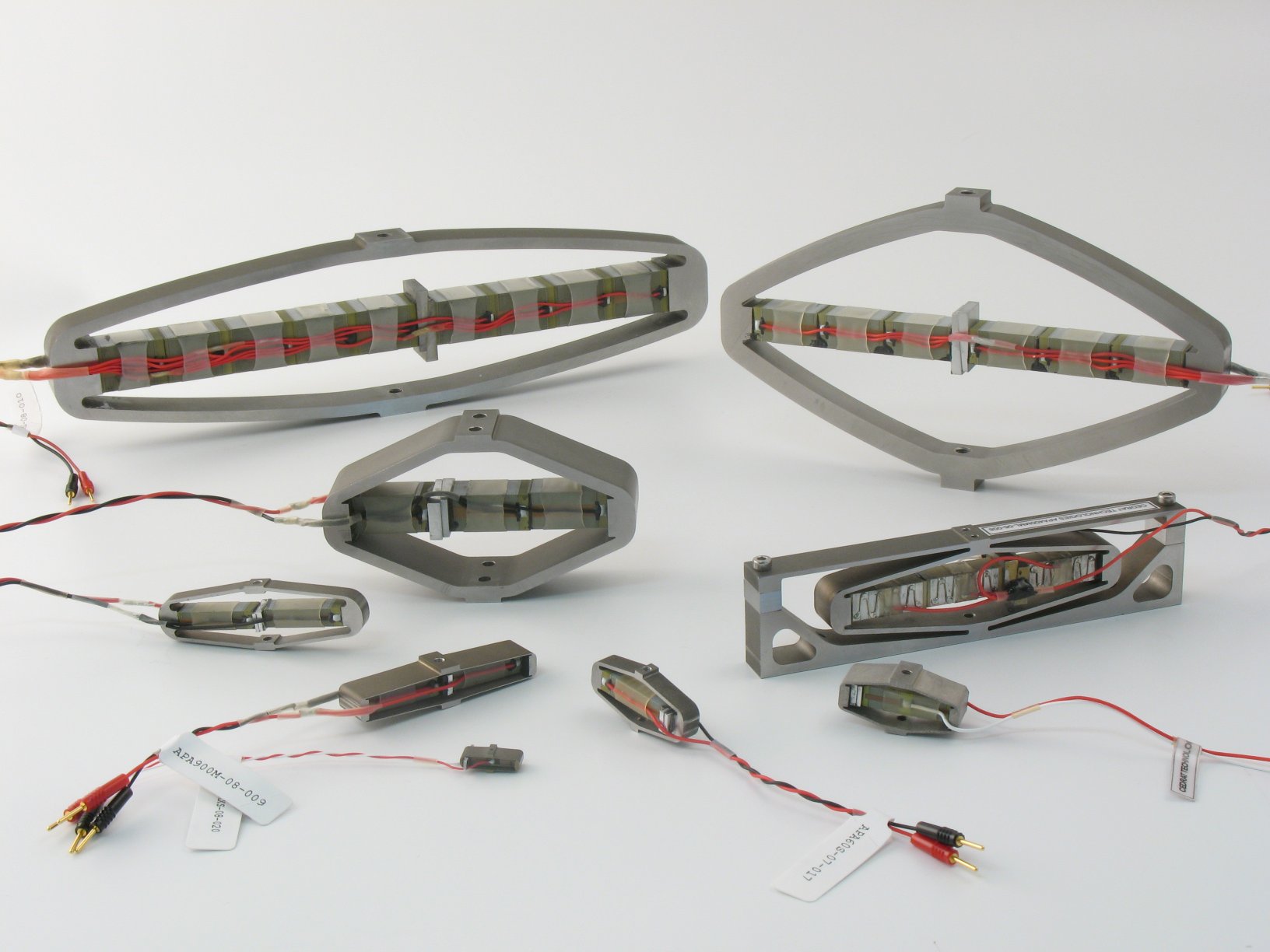
Amplified Piezoelectric Actuators:Static & Dynamic Applications
19 June 2023
Piezo actuators can be classified in three main categories: stack-type actuators, external/internal leveraged actuators and frequency-leveraged actuators (such as stepping motors and ultrasonic motors) [1]. Although Cedrat Technologies has developed several solutions using multilayered piezo ceramics and shell-based structures [2, 3], Amplified Piezo Actuators have today received the largest market interest.
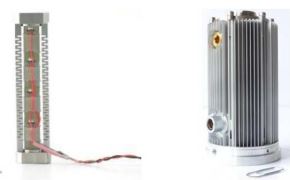
New developments in piezo actuators: Long stroke actuators and high power electronics
19 June 2023
In many cases piezoelectric actuators reach limitations in terms of maximum displacement and cycling frequency. Most amplified actuator technologies struggle to go over the millimeter of stroke. Furthermore certain closed-loop applications demand stroke measurement integrated into the actuator. While few amplifiers on the market can offer 20Amps current over a few 100ms, development of high power supply units runs parallel with actuator improvements. However with the introduction of high power supplies comes the problem of self-heating of the piezo ceramic. Finally extreme environmental conditions in terms of harsh conditions and high temperatures need to be addressed in order to open these markets for piezo actuators. Cedrat Technologies has been heavily investigating in solutions to overcome all of these drawbacks and these solutions are
presented here.