Publications
Categories
- (34)
- (9)
- (3)
- (144)
- (18)
- (7)
- (5)
- (8)
- (9)
- (17)
- (2)
- (104)
- (7)
- (15)
- (7)
- (2)
- (1)
- (6)
- (155)
- (20)
- (2)
- (5)
- (111)
- (35)
- (11)
- (4)
- (59)
- (18)
- (3)
- (7)
- (62)
- (18)
- (5)
- (24)
- (7)
- (12)
- (1)
- (2)
- (2)
- (1)
- (1)
- (14)
- (13)
- (4)
- (6)
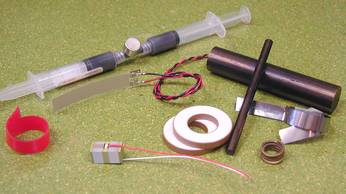
Giant dynamic strains in magnetostrictive actuators and transducers
19 June 2023
Magnetostriction occurs in the most ferromagnetic materials and leads to many effects [1,2]. The most useful one to refer to is the Joule effect. It is responsible for the expansion (positive magnetostriction) or the contraction (negative) of a rod subjected to a longitudinal static magnetic field. In a given material, this magnetostrain is quadratic and occurs always in the same direction whatever is the field direction. Giant Magnetostrictive Materials (GMM), especially Rare earth-iron discovered by A.E.Clark [3], feature magnetostrains which are two orders of magnitude larger than Nickel. Among them, bulk Tb0.3Dy0.7Fe1.9, called Terfenol-D, presents the best compromise between a large magnetostrain and a low magnetic field, at room temperature.
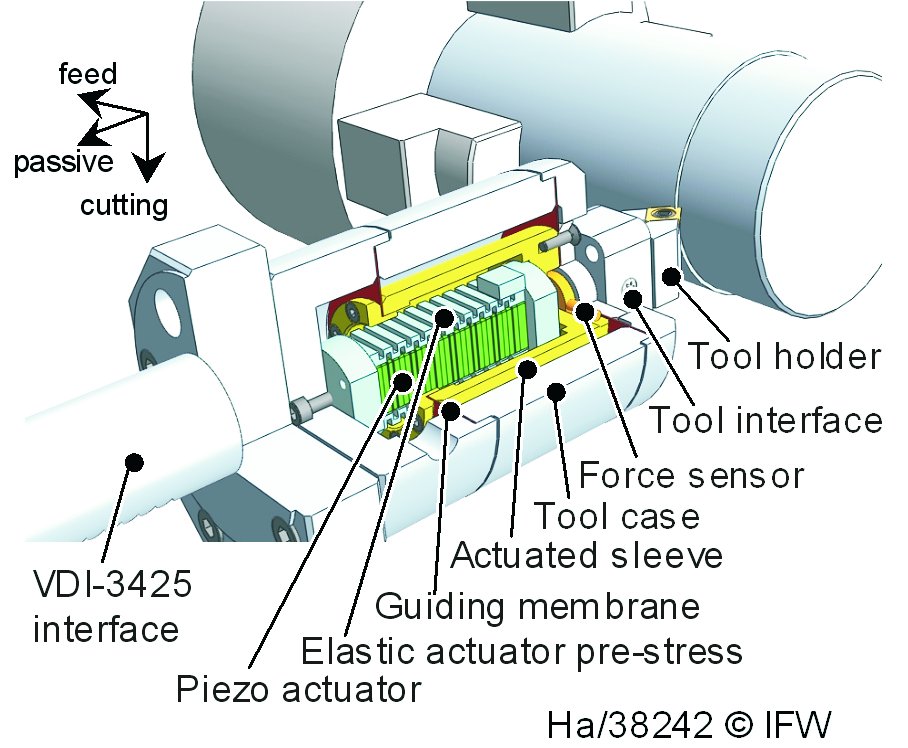
Tool adaptor for active vibration control in turning operations
19 June 2023
A tool adaptor with built-in active vibration damping device to dynamically stabilize the turning process is presented in this paper. It can be used in standard CNC-lathes and allows the usage of off-the-shelf tool heads. The vibration compensation system is based on a multilayer piezoactuator that is in collocation with a piezoelectric force sensor. An analogue controller based on the integral force feedback method is used for active damping.
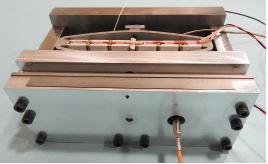
High performance synthetic jet actuator for aerodynamic flow improvement over airplane wings
7 June 2018
In the framework of a French National Program, the project ASPIC aims at using synthetic jet actuators to improve aerodynamic performance of aircrafts. The partnership between Cedrat Technologies (CTEC) and the French Aerospace Lab (ONERA) in this project has led to design, manufacture and test a high efficiency innovative synthetic jet actuator. This device relying in part on an ONERA patent is actuated by a CTEC amplified piezoactuator (APA). Its aim is to provide a high speed synthetic jet compatible with flow control application on aircrafts or any other vehicle. Latest available test results and experimental performances of the ASPIC synthetic actuator are presented in this document: in particular, a peak exit velocity of 135m.s-1 during suction, and of 150m.s-1 during blowing, with an optimal actuation frequency bandwidth between 200 and 300Hz.
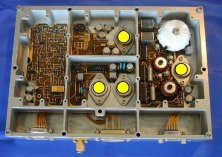
Driving control electronics piezoelectric actuators space applications
19 June 2023
Piezoelectric mechanisms are more and more used in space applications requiring precise positioning functions for scientific payloads or optical functions. Indeed, piezoelectric actuators are generally deemed of being good candidates for driving and control compact mechanisms.
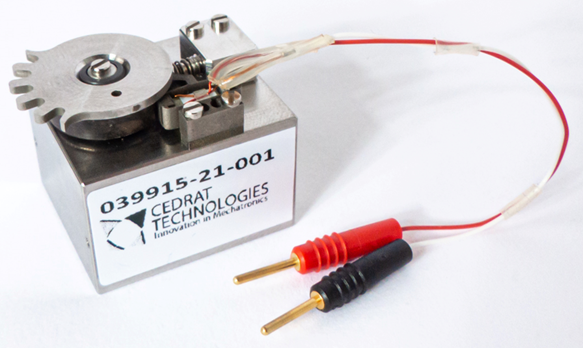
High power density Piezo motors for critical environments
8 September 2022
Piezoelectric motors offer many advantages for applications in numerous industrial sectors. The requirements for which these solutions are developed are focused on their main advantages such as non-magnetic and radiation compatibility, high force/volume ratio, good unpowered stall force and low power consumption. Such applications are typically concerned by exotic working conditions on which the piezoelectric motors still need to improve regarding the technological readiness level.

High power force oscillator and drive electronics
19 June 2023
This paper presents the development of one amount the largest piezo actuator ever designed based on low voltage PZT. This actuator is able to provide more than 20kN of force in dynamic operation (60kN in static operation). The purpose of low frequency vibration generation is to improve the quality of parts production in the field of manufacturing and machining process.