Publications
Categories
- (34)
- (9)
- (3)
- (144)
- (18)
- (7)
- (5)
- (8)
- (9)
- (17)
- (2)
- (104)
- (7)
- (15)
- (7)
- (2)
- (1)
- (6)
- (155)
- (20)
- (2)
- (5)
- (111)
- (35)
- (11)
- (4)
- (59)
- (18)
- (3)
- (7)
- (62)
- (18)
- (5)
- (24)
- (7)
- (12)
- (1)
- (2)
- (2)
- (1)
- (1)
- (14)
- (13)
- (4)
- (6)
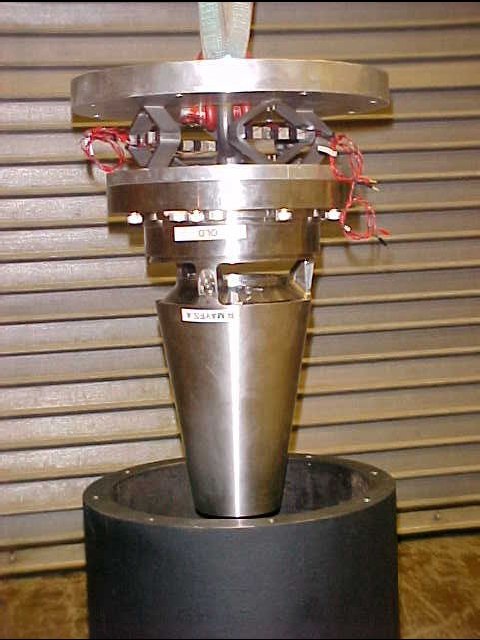
Testing of amplified piezoelectric actuator in a combined vibration and acceleration
19 June 2023
Sandia National Laboratories has previously tested a capability to impose a 7.5 g-rms (30 g peak) radial vibration load up to 2 kHz on a 25 lb object with superimposed 50 g acceleration at its centrifuge facility. This was accomplished by attaching a 3,000 lb Unholtz-Dickie mechanical shaker at the end of the centrifuge arm to create a âVibrafugeâ. However, the combination of non-radial vibration directions, and linear accelerations higher than 50gâs are currently not possible because of the load capabilities of the shaker and the stresses on the internal shaker components due to the combined centrifuge acceleration.
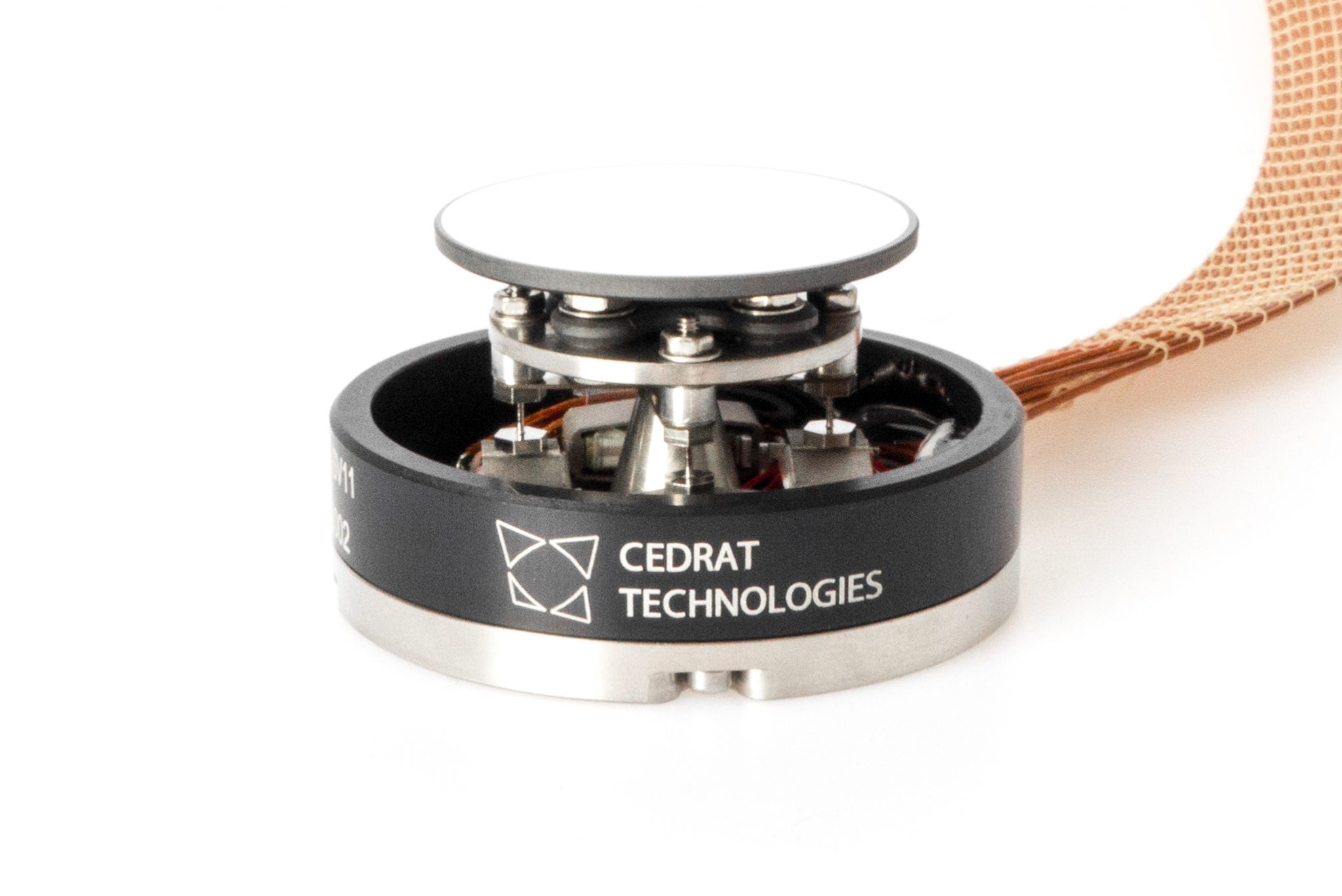
Development of magnetic fast steering mirror prototype for optical pointing applications
7 June 2018
Fast Steering Mirrors are core products continuously developed by Cedrat Technologies (CTEC) for optical pointing applications, for Space, and Optronic domains. During the last decade, main development efforts where focused on piezoelectric mechanisms technology, in order to achieve ultra-high frequency bandwidth control performance over small angle strokes. New applications under maturation in Europe, such as laser optical communication, require much higher angle strokes compared to the existing state of the art, which cannot be easily achieved by piezoelectric technology. Therefore CTEC is focusing on the development of a new Fast Steering Mirror family based on high angle stroke magnetic actuators. This paper presents this new steering mechanism concept, and the prototype performance results expected.
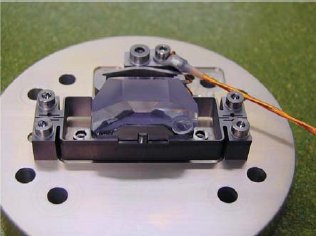
The design and qualification of the piezo actuated
19 June 2023
As part of the Lisa Technology Package (LTP) on board the LISA-PATHFINDER spacecraft, the LISAPATHFINDER interferometer is of the heterodyne Mach-Zehnder type. It requires as input two light beams derived from the same source but with a small frequency difference (a few kHz). These two optical beams are produced in the Laser Assembly (LA) via the “Laser Modulation Unit” (LMU). The LMU includes an optical bench, two Acousto-Optic Modulators and two Optical Delay Lines [1].
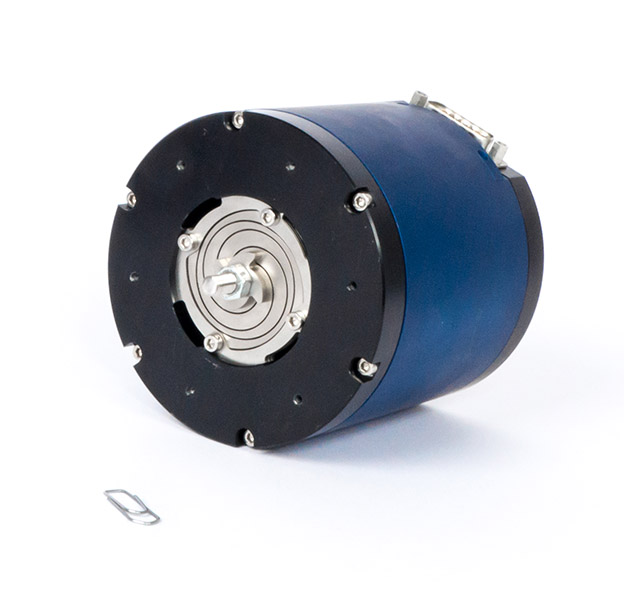
Development of the plain bearing and flexure bearing MICA300CM actuator
7 May 2018
The MICATM linear actuator family (Moving Iron Controllable Actuator) is being continuously improved at CEDRAT TECHNOLOGIES (CTEC) for applications needing high controllable stroke, force, and power. The MICA300CM is a new actuator model, having improved configuration based on cylindrical shape. A first version based on plain bearing offers up to 12mm stroke and 300N continuous force with a weigh of only 3kg. A second version is based on new frictionless flexure bearings. The former one is especially designed to achieve zero maintenance over several years of operation, with high efficiency, infinite resolution, and high controllability performance. This version of the MICA300CM has been derived to offer a proof mass configuration, for vibrationcancellation applications on machining processes. A latest version is also currently under design, and prototyping, specifically for reciprocating power piston applications, such as compressors, pressure wave generators, and pumps. Its high efficiency, ultra-long lifetime capability, and compactness, makes it perfectly suitable for embedded thermal machines based on Stirling, Joules Thomson, and Rankin Thermodynamic cycles. This paper presents this 4 design concepts, their test results and perspective for applications.
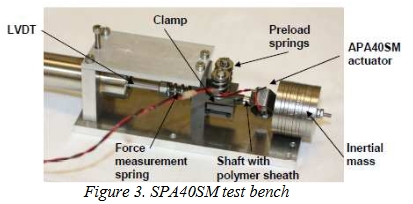
Thermal vacuum behaviour of a stepping piezo actuator
19 June 2023
The presented work illustrates the design of a new high force Stepping Piezoelectric Actuator (SPA) and describes its Thermal Vacuum testing as performed by ESTL, in order to investigate SPA compatibility with vacuum environment within a wide temperatures range; from +60°C down to -180°C. A dedicated test bench was designed, in order to check motor force and speed for all performed tests. Instrumentation, testing and observations about tribological behaviour of friction interface have been realized by ESTL, showing interesting perspectives.
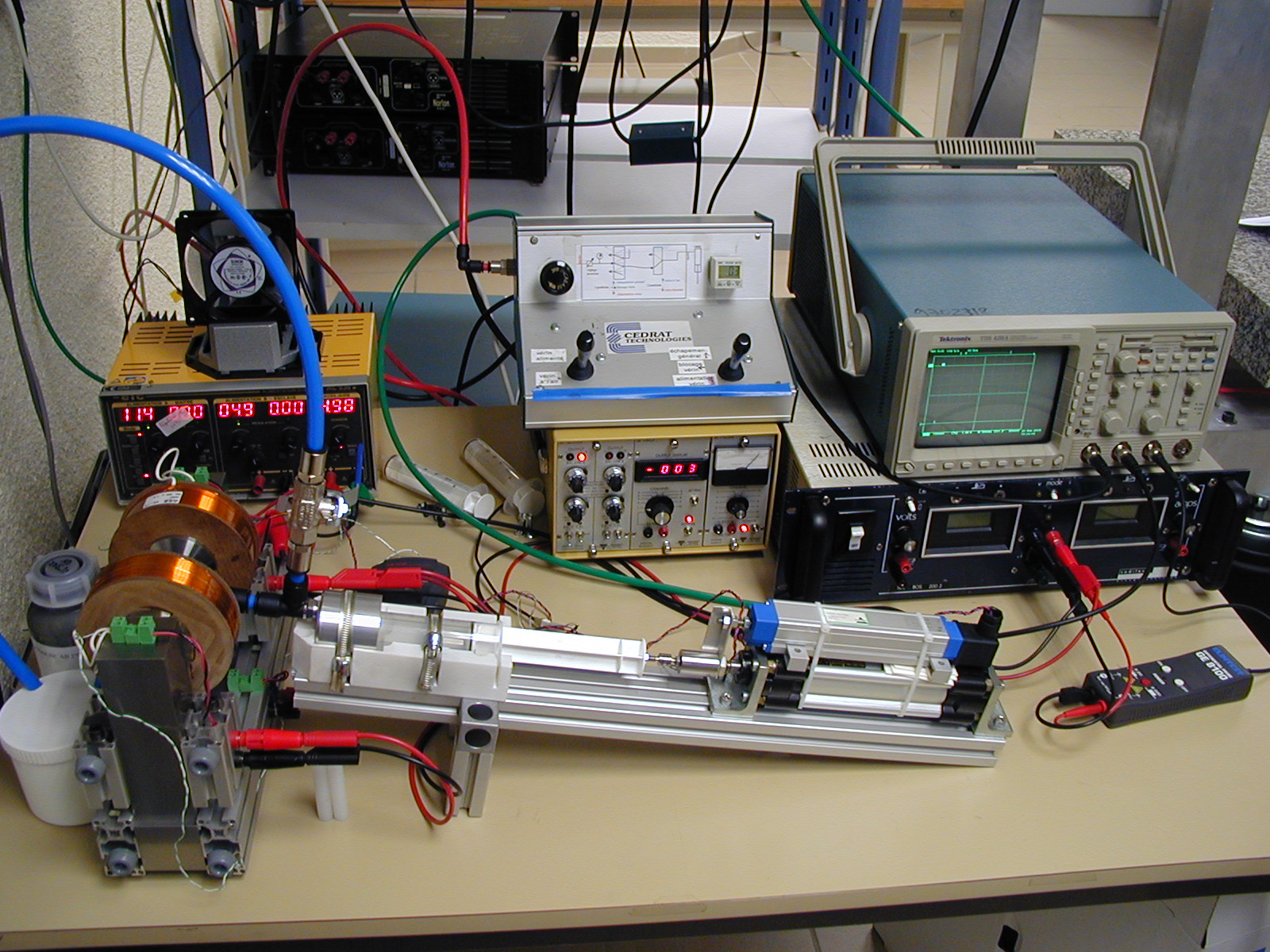
Characterisation of magneto-rheological fluids for actuators applications
19 June 2023
Magnetorheological fluids (MRF) are magnetically controlled fluids and they find more and more industrial applications in actuation functions. These include shock absorbers, semi-active dampers, clutches, brakes, haptic actuators & devices. Several of these applications have been studied by Cedrat Technologies for its industrial customers, and a device-oriented test bench has been developed in order to characterise the magneto-mechanical properties of MRF such as the magnetisation curve, the yield stress âŠ.