Publications
Categories
- (34)
- (9)
- (3)
- (144)
- (18)
- (7)
- (5)
- (8)
- (9)
- (17)
- (2)
- (104)
- (7)
- (15)
- (7)
- (2)
- (1)
- (6)
- (155)
- (20)
- (2)
- (5)
- (111)
- (35)
- (11)
- (4)
- (59)
- (18)
- (3)
- (7)
- (62)
- (18)
- (5)
- (24)
- (7)
- (12)
- (1)
- (2)
- (2)
- (1)
- (1)
- (14)
- (13)
- (4)
- (6)
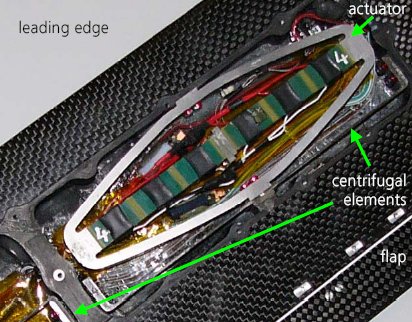
ABC Rotor blades: design, manufacturing and testing
19 June 2023
ABC is the acronym for ââActive Blade Conceptââ and represents a 38% Mach scaled model rotor of the Advanced Technology Rotor (ATR) of Eurocopter Germany (ECD, [4]). In contrast to the ATR the model rotor is fully articulated. Specifically, it is equipped with a flap at the trailing edge of each blade, which is driven by a piezoelectric actuator. The ABC project is a cooperation between the French ONERA and the German DLR within the research concept ââThe Active Rotorââ.
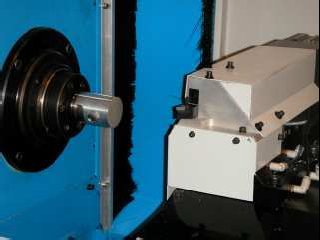
Actuators in adaptronics: piezoelectric actuators
19 June 2023
Piezoelectric actuators have increased their number of application in adaptronics over the past decade [1]. They can be used with several drive and control strategies and they are more adapted to mechatronics applications requiring bandwidth, accuracy and/or lightweightness. The purpose of this paper is to recall the different existing piezo actuators, the different drive and control techniques and finally review several applications in machine tools, optics.
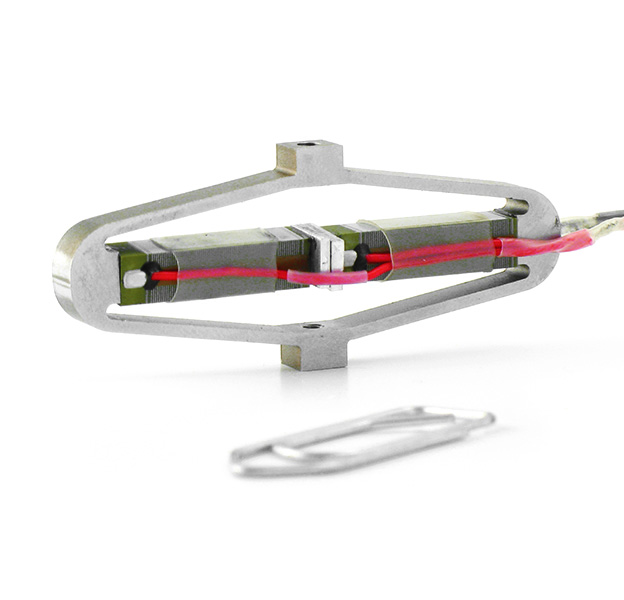
Constant gradient elastography with optimal control RF pulses
7 November 2019
This article presents a new motion encoding strategy to perform magnetic resonance elastography (MRE). Instead of using standard motion encoding gradients, a tailored RF pulse is designed to simultaneously perform selective excitation and motion encoding in presence of a constant gradient. The RF pulse is designed with a numerical optimal control algorithm, in order to obtain a magnetization phase distribution that depends on the displacement characteristics inside each voxel. As a consequence, no postexcitation encoding gradients are required. This offers numerous advantages, such as reducing eddy current artifacts, and relaxing the constraint on the gradients maximum switch rate. It also allows to perform MRE with ultra-short TE acquisition
schemes, which limits T2 decay and optimizes signal-to-noise ratio. The pulse design strategy is developed and analytically analyzed to clarify the encoding mechanism. Finally, simulations, phantom and ex vivo experiments show that phase-to-noise ratios are improved when compared to standard MRE encoding strategies.
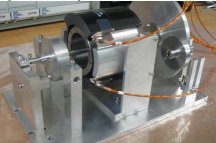
Limited Angle Torque for fine angular positioning
19 June 2023
A Limited Angle Torque (LAT) actuator has been designed by Cedrat upon request of the European Space Agency (ESA) for fine pointing applications based on gimbals assembly. The required angular stroke for this application is 13°. Other required features are controllability, high resolution, no micro vibration. Therefore the selected concept is a coil-redounded electromagnetic actuator using Lorentz force. The functional test shows that the generated torque is linear until 200mN.m, but torques up to 300mN.m are achievable.
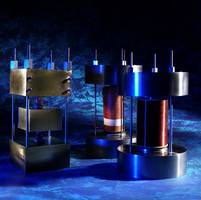
Actuators, transducers and motors based on giant magnetostrictive materials
19 June 2023
Rare earth-iron magnetostrictive alloys, especially Terfenol-D, feature “giant” magnetostrains: static strains of 1000-2000 ppm and dynamic strains of 3500 ppm are reported.
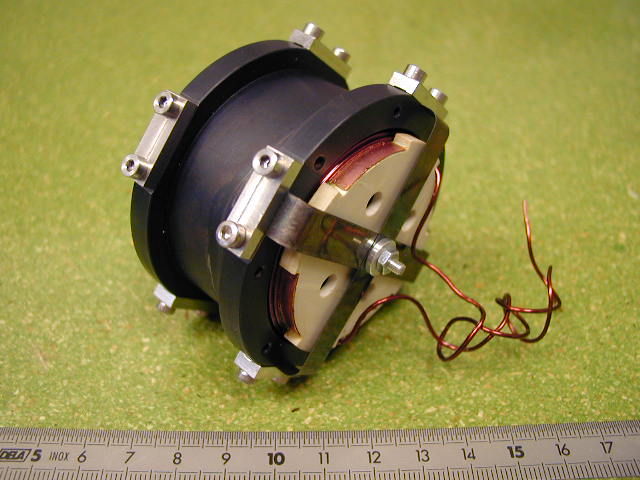
Space compliant mobile voice coil actuator
19 June 2023
A moving coil actuator for high precision positioning and compatible with space technology specifications has been designed and successfully tested. General space technology requirements are the use of no degassing material, no lubrication, low mechanic time constant, low electrical power consumption, and thermal energy evacuation through radiating and conducting exchanges (no convection because of operation in vacuum environment). These specifications have been accounted in the design, the realisation and the test of a successful prototype: Thanks to a good design of thermal drains, the actuator presents a high force versus weight ratio.