Publications
Categories
- (34)
- (9)
- (3)
- (144)
- (18)
- (7)
- (5)
- (8)
- (9)
- (17)
- (2)
- (104)
- (7)
- (15)
- (7)
- (2)
- (1)
- (6)
- (155)
- (20)
- (2)
- (5)
- (111)
- (35)
- (11)
- (4)
- (59)
- (18)
- (3)
- (7)
- (62)
- (18)
- (5)
- (24)
- (7)
- (12)
- (1)
- (2)
- (2)
- (1)
- (1)
- (14)
- (13)
- (4)
- (6)
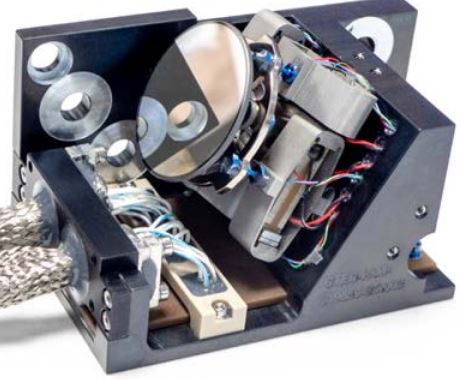
Fast and fine Steering Mirrors based on piezoelectric & magnetic actuator technologies for Air and Space
8 August 2022
This review presents CEDRAT TECHNOLOGIES (CTEC) solutions developed for more than 20 years for Fast & fine Steering Mirrors (FSM) as required in air, space, defence & other embedded or demanding applications: Typical appli-cations are for example Lidar, free space optical communication (FSO) and Laser interferometry.
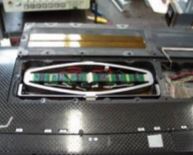
Active flap device for helicopters based on Cedrat Amplified Piezoelectric Actuators
19 June 2023
A project called RPA (Rotor Ă Pales Actives) was launched three years ago to study the possible benefits of implementing active trailing edge flaps on a helicopter main rotor. The main objectives of this project are to decrease BVI noise in descent flight and improve the dynamic behavior of the rotor throughout the largest possible flight domain. After a first phase dedicated to the design of the best flap configuration at scale 1, the second phase of the project deals with the design of a wind-tunnel scale model of a rotor equipped with active flaps. An off-the-shelf piezo-electric actuator is used together with a specific patented flap-driving mechanism. Such an active device was tested under centrifugal loads as well as under aerodynamic loads in order to prepare future wind-tunnel tests. The results obtained under centrifugal loads allowed to clear the active device but the aerodynamic testing showed that some improvements were needed. Corresponding modifications are under way to fully clear the active device to be used on a complete rotor model.
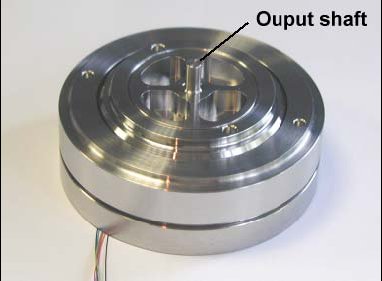
Rotating piezoelectric motors for high precision positioning & space applications
19 June 2023
Piezo-electric motors have been successfully developed for various applications like autofocus drives in camera lenses and handling equipment for semiconductor production. Their high speed and accurate positioning capability, combined with a favourable holding torque in unpowered condition, make piezomotors also very attractive for actuation purposes in spacecraft mechanisms. The paper introduces a new concept of a versatile ultrasonic piezomotor. The testing campaign carried out on the designed rotating piezomotor has validated the vacuum compatibility and the lifetime of the motor in air.

Ski embbeded piezo system
19 June 2023
Since many years, the field of active control of vibrations has been growing up and many new applications using smart actuators have been developing. In 2003, CEDRAT TECHNOLOGIES in collaboration with SKI ROSSIGNOL initiated a project supported by ESA where these concepts (smart material and active control of vibration) were adapted and applied on a ski structure. The project aim was to damp the large modes of vibrations keeping the robustness of the control and the static loads during the ski ride.

A new amplified piezoelectric actuator for precise positioning and active damping
19 June 2023
Two typical characteristics of direct piezoelectric actuators are displacements of ten micrometers and high stiffnesses. recently, multilayers actuators have been improved, and they now display strains of approximately 1200ppm at low excitation levels (less than two hundred volts). Thus, they are well suited to perform precise positioning of optical devices. But for industrial needs, this performances is still insufficient for positioning devices with larger displacements (in the range of several hundred micrometers).
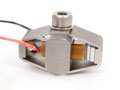
Active washer for smart mechanical linkage
9 December 2017
Bolted connection is the most common way to assemble mechanism. It is widely used in transport domains, such as aerospace, rail, aircrafts⊠Ensuring that the minimum torque value is always present in the assembly is one of the main maintenance tasks for those components. A possible way to carry out those actions is to implement active component in the bolted assembly. A solution is proposed in this document. Construction, potentialities, performances (based on lap-joint demonstrator) and limitations are identified and confronted to other techniques.