Publications
Categories
- (34)
- (9)
- (3)
- (144)
- (18)
- (7)
- (5)
- (8)
- (9)
- (17)
- (2)
- (104)
- (7)
- (15)
- (7)
- (2)
- (1)
- (6)
- (155)
- (20)
- (2)
- (5)
- (111)
- (35)
- (11)
- (4)
- (59)
- (18)
- (3)
- (7)
- (62)
- (18)
- (5)
- (24)
- (7)
- (12)
- (1)
- (2)
- (2)
- (1)
- (1)
- (14)
- (13)
- (4)
- (6)
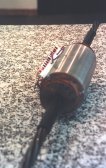
Capteur électromagnétique effort et applications
19 June 2023
This article deals with a stress sensor for cables which has been designed, built and test. it is based on a special magnetostrictive effect of ferromagnetic materials as high elastic limit steels used for bridge cables or prestressed concrete.
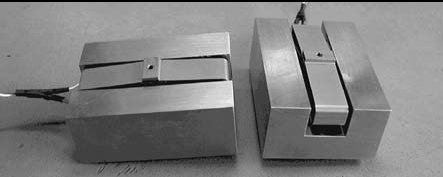
Vibration energy harvesting in aircraft using piezoelectric actuators
19 June 2023
In the aicrft vehicle, a part of the produced energy is transformed into mechanical vibration energy losses. This rue is more than ever true when the need for electrucal energy is a crucial problem. So, systems which are able to transform the mechanical energy in a scavenged electrical energy are very interesting.
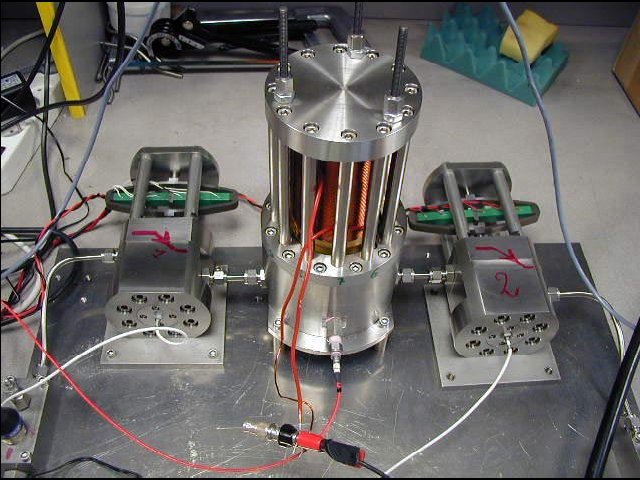
Electro-fluidic components based on smart materials for aircraft electro-hydraulic
19 June 2023
In the context of a more electrical aircraft, in order to explore the feasibility of non usual solutions, electro-fluidic components based on smart materials and new Electro-Hydraulic-Actuators (EHA) concepts, based on active valves and magnetostrictive vibrating pump, have been studied. Active valves based on different magnetostrictive and piezoelectric actuators have been designed, realised, tested and compared. The magnetostrictive version uses a new Amplified Magnetostrictive Actuator (AMA) based on a stack of Giant Magnetostrictive Materials (GMM) and placed inside an elliptical amplification ring.
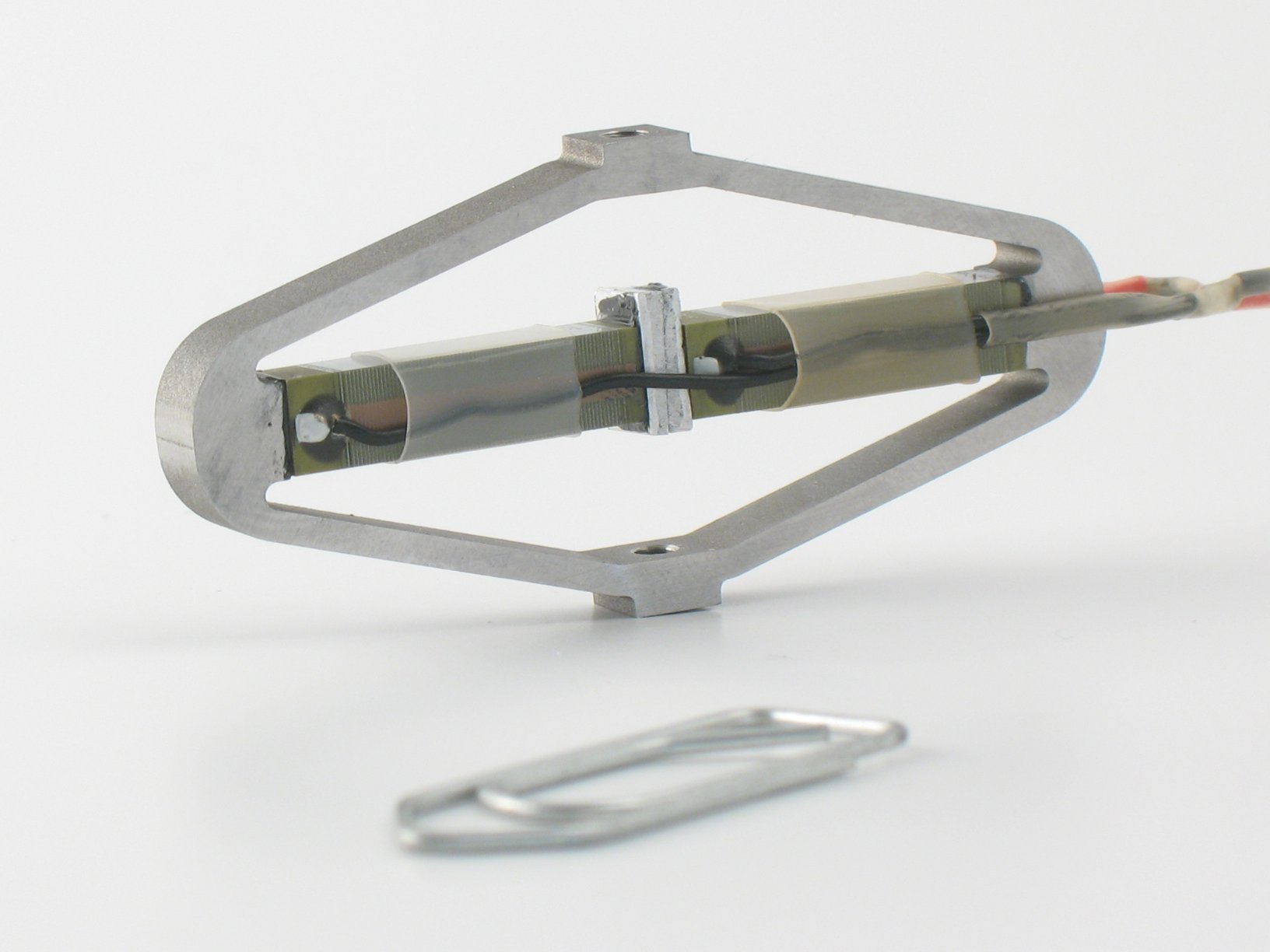
Vibration isolation of an extended object
19 June 2023
An increasing number of applications required a very high level of precesion: semiconductor manufacturing, atomic force microscopy, scanning probe microscopy, machine tool, etc. Such high precision can only be reached in very stable environments. the standard procedure is to mount the sensitive equipment on a heavy isolating stage, sometimes referred to as optical table, which can be either passive or active.
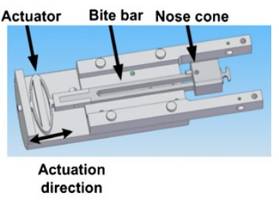
Viscoelastic properties of the ferret brain measured in vivo at multiple frequencies by magnetic resonance elastography
19 June 2023
Characterization of the dynamic mechanical behavior of brain tissue is essential for understanding and simulating the mechanisms of traumatic brain injury (TBI). Changes in mechanical properties may also reflect changes in the brain due to aging or disease. In this study, we used magnetic resonance elastography (MRE) to measure the viscoelastic properties of ferret brain tissue in vivo.
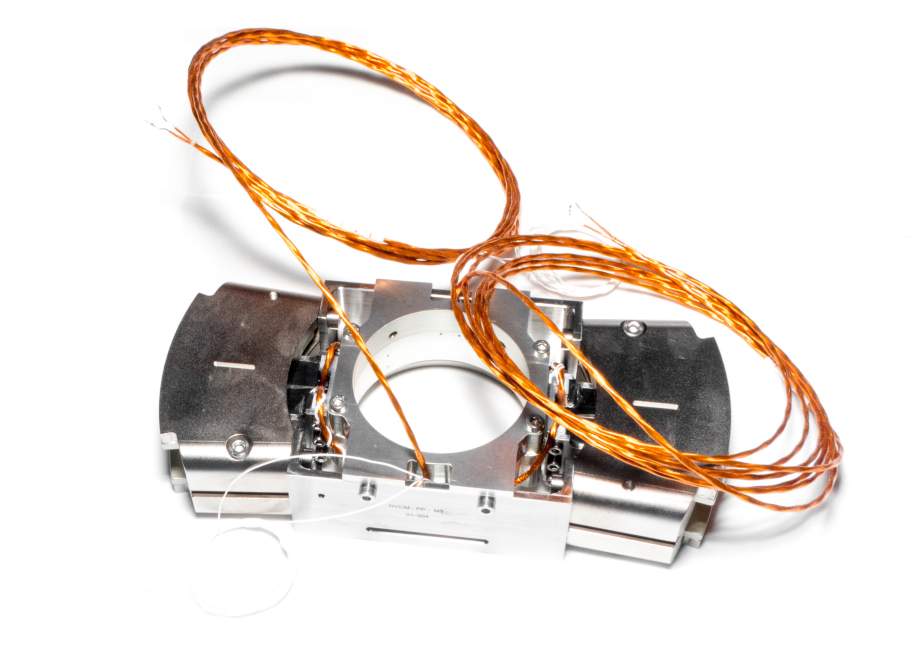
Voice coil actuators for two MTG instruments
19 June 2023
While Cedrat Technologies has been active in space for more than 20 years with piezoelectric mechanisms, we have also been increasingly involved over the last few years in the development of magnetic actuators for space projects. In this paper, a focus is made on the case of magnetic actuators that are developed in the frame of the Meteosat Third Generation (MTG) project. The first one is the Scan Assembly (SCA) actuated by Rotating Voice Coil Motors (RVCM) for the East/West (E/W) axes and the North/South (N/S) axes developed in collaboration with Sener and the second one is the Voice Coil Motor (VCM) developed in collaboration with CSEM for the Corner Cube Mechanism (CCM)