Cedrat Technologies (CTEC) is developing a new generation of Eddy Current Sensors (ECS) that will improve the observability of displacements and therefore the bandwidth control performance and speed compared with Strain Gauges (SG).This new development also makes it possible to get more compact mechanisms than with capacitive sensors.
Following the current qualification phase, this new technology will be offered to our customers in mechanisms such as the Piezo Fast Steering Mirror TT60SM, the Magnetic Fast Steering mirror M-FSM45 and XY stages. This development meets the needs of our space and defence customers to increase dynamic performances while reducing the size of mechanisms.
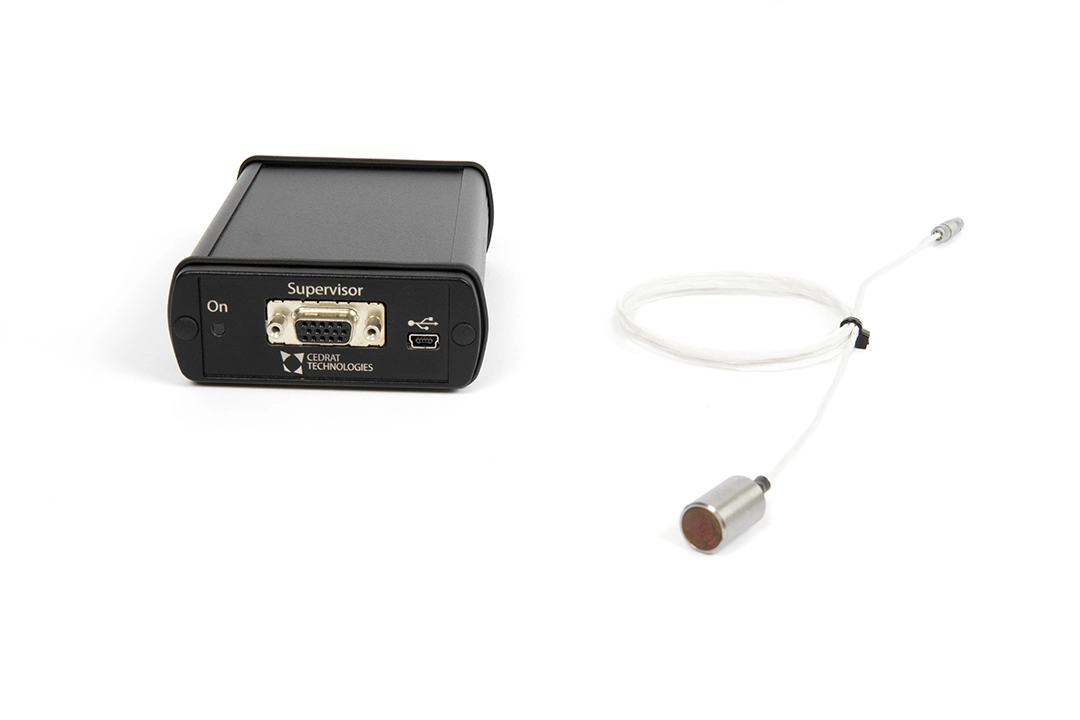
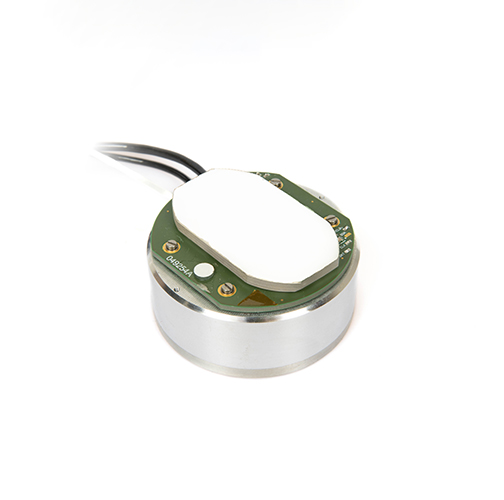
CTEC actuators may include positioning sensor options in a compact design. Strain gauge (SG) sensors are well-suited for this compactness due to their small size and accurate response. SG sensors provide indirect motion measurement because they are implemented on the piezo ceramics, rather than directly at the tip of the motion mechanism. Controlling such systems may require a specific control law to account for the transfer function between the SG sensor and the mechanism’s tip. This observability is fundamental in all control loops. However, for certain mechanisms, this solution is not efficient enough, and specific contactless metrology must be considered to improve sensor performance.
CTEC has already integrated such sensors directly into their mechanisms (e.g., PCB-built Eddy current sensors or accelerometers) or in specific optical benches (e.g., Photodiode Sensing Detectors). One key advantage is the ability to control the actual position of the payload, leading to more efficient control with greater performance capabilities.
Application: TT60SM equipped with an ECS sensor
On Figure 1, the ECS response above the first resonance frequency is more detailed and accurate than with SG sensors. This enables the implementation of advanced control techniques as previously described. Our solution integrates an electronic front end close to planar coil probes (we offer both single and differential configurations). This compact solution—probes plus narrow electronics—minimizes an inherent issue with eddy current sensors, namely the parasitic effects of the cable, which reduce overall accuracy. Additionally, the signal conditioning is immune to electromagnetic compatibility (EMC) issues .